Kal Plastics deploys Universal Robot trimming cobot for a fraction of the cost and lead time of a CNC machine, cuts trimming time nearly in half and reduces late shipments to under 1% — all while improving employee safety and growth opportunities. #close-up-on-technology
As the first known thermoformer to use a collaborative robot (cobot) for trimming, Juliet Oehler Goff, president and CEO of Los Angeles-based Kal Plastics, knew she was blazing a trail for others. “It was arguably kind of crazy because no one had ever done it before, so I took a huge risk,” she says, adding with a smile: “I don’t go to Vegas, but I gamble nine to five.” Taiwan Thermoforming Machine
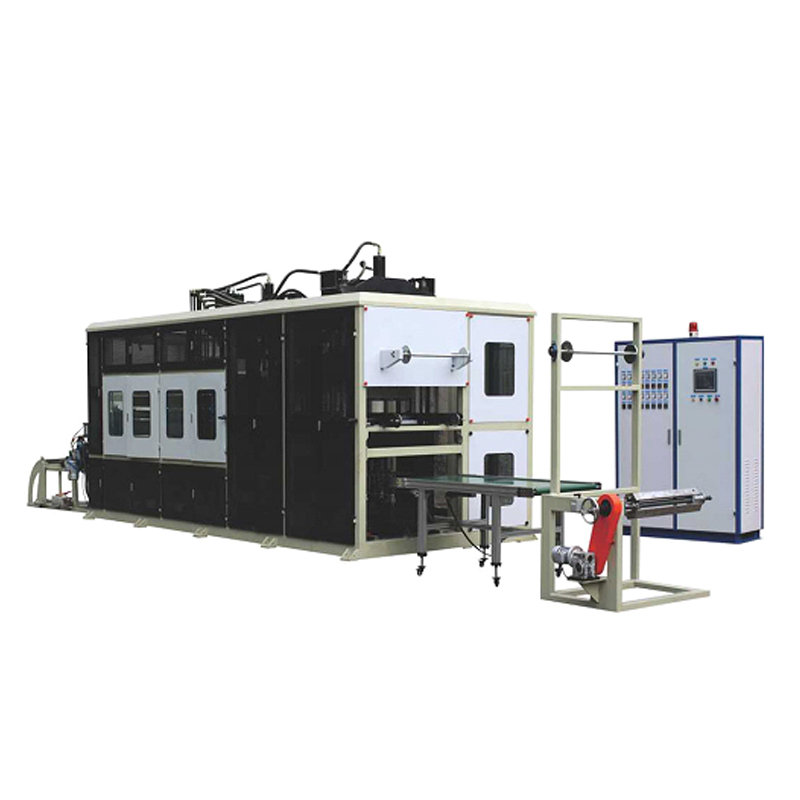
Over the years, 5-axis CNC routers had replaced hand-trimming for most thermoformers. More recently, Goff had watched other processors use large industrial robots to finish-trim molded parts, but she wasn’t convinced that was an option for her. For a business like Kal Plastics, the initial price point of industrial robots and their required safety caging was too high, not to mention the programming costs.
“You end up having to have a skill set under your roof that’s very expensive. That’s a risk for a small business,” she explains. After talking to colleagues, she heard behind the scenes that many of those who had tried industrial robots found that they didn’t work well for their applications and that they wouldn’t buy them again.
Goff is also a director and member of the R&D committee of the Society of Plastics Engineers’ (SPE) Thermoforming Division. In that role, she had been involved in numerous discussions about the state of robotics, particularly cobots, and their application in the industry. When Kal Plastics needed to replace a CNC machine that was nearing the end of its useful life, Goff was presented with an ideal opportunity. She set out to research the use of cobots for her own business and agreed to share her findings at the organization’s national conference.
Kal Plastics CEO Juliet Oehler Goff and consultant Dan Sproles inspect finished parts as the cobot finishes trimming. The cobot offers high accuracy and consistency, and has helped reduce late shipments to under 1%. Photo Credits: Universal Robots
As a contract manufacturer, Kal Plastics produces a wide range of parts with varying complexity and tolerances. Goff looked for low-hanging fruit for the initial cobot deployment: parts that presented safety or productivity issues with hand-trimming, and that could be produced on less-expensive equipment to boost competitiveness. Once she could prove the cobot worked, she knew there were other jobs that fit those criteria.
“I did my homework and found that Universal Robots was the global leader in the collaborative robot space,” Goff says. “They came out and gave us a demonstration and, when I looked at the numbers, they were really attractive. I was looking at getting another five-axis CNC router, and at the time it would have been a $250,000 investment and I would have waited 12 months to take delivery. When I met with UR, I was quoted two weeks to get the equipment, and the entry point was a quarter or a fifth of the cost.”
During the course of her research, Goff hired Dan Sproles, a consultant and another director for SPE Thermoforming, to help improve overall operations. From his initial skepticism, Sproles has also become a champion of lightweight, cost-effective and easy-to-program UR cobots.
Sproles says, “If you’re a thermoformer that’s been in business for 50 years or five months, a cobot is a perfect fit. Because if you can’t afford a new CNC, you can afford this. And you can afford someone that’s going to basically take a tablet and program it. So your bang for your buck — it’s the robot.”
Goff concurs, “It would be foolish for other processors not to consider adding this to their operation. They’d be really missing out on a smart business decision.”
Before installing the collaborative robot, forming and rough trimming took place in the thermoforming cell, and then the parts had to be transferred to the CNC router in another part of the plant. The Kal Plastics facility is housed in multiple older buildings, so moving parts was disruptive and added production time. It also presented opportunities for damage or safety hazards as parts stacked up waiting in queues.
“If you’re a thermoformer that’s been in business for 50 years or five months, a cobot is a perfect fit.”
The initial task identified for the cobot is a complex trim of a four-cavity mold. The ability to install the cobot into the same work cell alongside the thermoformer inspired Sproles to describe it as a “cell manufacturing dream.” Formed parts now come off the thermoformer and are immediately rough cut to separate them. They are then delivered directly to the cobot, which can trim two pieces in each setup. The cobot takes nearly half the time of hand-trimming, and provides greater accuracy and consistency.
The deployment has two routers mounted on the robot arm — one with a standard router bit and one with a larger saw blade. The advantage is that the routers are the same commercial tools used for hand trimming. They are inexpensive and available off-the-shelf at any hardware store, so there is no expensive replacement or downtime due to tooling issues. Balancing the two heavy routers as they rotated around the part presented early challenges that were solved by mounting the robot arm overhead on a gantry to reduce pressure on the robot joints and improve accuracy.
The efficiency of the new work cell has already paid off. “The robot has basically taken over all of the overflow that we had to do by hand,” Sproles explains. “In the past, we always had to juggle back and forth on the CNCs just to make delivery dates. We introduced the cobot: now there’s no more overtime and we can ship on time. I would say late shipments have dropped to less than 1%.”
“It would be foolish for other processors not to consider adding cobots to their operation.”
Now that the cobot has been proven, Goff is looking forward to implementing newer, larger cobots in other workstations, and for processes beyond trimming. Ultimately, she would love to “form, trim, palletize, out-the-door” from complete, automated work cells. Until then, the flexibility of the relatively lightweight cobot is an added bonus. Unlike a CNC, which requires a large dedicated space, permanent installation and a three-phase, 480-V power source, the gantry and UR10e cobot along with the fixture table can be moved anywhere in the plant as needed, as long as there is a standard 110-V power outlet.
The cobot’s ease of programming was a big deal, explains Sproles. “If I bought a regular CNC, regular robot, I’m going to spend thousands of dollars training that person, not knowing if they’re going to be here tomorrow.” The expense and risk of training workers in traditional programming is significant for small businesses, who are already facing difficulties in retaining skilled workers in a competitive labor environment.
With the UR cobot, José Luis, a valued Kal Plastics operator, was able to learn the basics of programming using the free online UR Academy classes, which he could access in his native Spanish. He then attended two sessions of affordable, hands-on training. That was all it took for him to be able to create new programs, change tools and make adjustments as needed.
The extended reach of the UR10e cobot, which is top-mounted on a gantry, means it can trim two parts per setup, cutting trimming time nearly in half compared to previous manual trimming.
Luis recognizes that technology is evolving and his past skills will not necessarily be the skills he needs in the future, so he is eager for the opportunity to learn. He says, “My job is more interesting because the manufacturing process is really improved, and the robot provides me a safer workplace.”
Goff is thrilled to have a way to retain and advance her valued employees. “It gets your workforce excited because it’s different, it’s cool, it’s unique,” she says. “When you get someone that’s younger, that’s hungry, you want to find a way to satisfy their hunger and keep them interested and motivated.” She adds, “It’s been a treat to watch José grow in this role, and elevate himself.”
“My job is more interesting because the manufacturing process is really improved, and the robot provides me a safer workplace.”
Luis is already scheduled for a Master Programmer class, where Sproles expects he will gain additional insight to make the robot cell even more profitable and repeatable, and to program it for any new jobs the company brings in.
Goff describes California as a tough state for manufacturing. Challenges include high costs of labor, occupancy and energy, as well as a regulatory environment that presents additional workforce challenges. “It’s a no-fault state for Workers’ Compensation injuries,” she explains. “It’s the right thing to provide a safe workplace environment, but it’s also a fiduciary responsibility to try to avoid having those incidents occur. So we’re always looking for ways to work safer, work smarter, work faster.”
Along with those challenges, Goff is also dealing with labor issues that are common across the country: workers who are less interested in manufacturing jobs. Labor and safety were key drivers for Kal Plastics to become an early automation adopter. “Necessity is the mother of invention,” Goff states.
Kal Plastics cleverly balanced two commercial routers on the cobot arm, using a saw blade and a standard router. The ability to use inexpensive, off-the-shelf routers, which can be purchased at any hardware store, is a strong advantage of the UR cobot.
The job that the UR cobot now handles used to be hand-trimmed. Sproles says, “In this plant, there are two people that can route parts. So if you brought in a job that had to be hand-routed, you’ve got those two people and you’re locked in because that’s all they can do.” Now those employees can be redeployed to safer, more valuable tasks and production isn’t limited to the availability of those workers, giving the company better production flexibility.
When Goff began her research, her workforce was afraid that robots were going to replace their jobs. She told them, “Listen, you don’t get it, guys. I want you to be safe. I want you to work smart. I don’t want you to just rely on your hands; I want you to rely on your knowledge and skills. If we can get our work environment to a point where you’re more of a QC operator than a machine operator, that’s a win for everybody.”
After working with the cobot, her workers’ attitudes have completely changed. Goff says, “Once everyone settled down and they saw how this thing worked, it was like, ‘Why didn’t we do this sooner?’”
Compact, flexible and configurable robotic system is said to be the first to enable thermoformers to fully automate product handling after a non-servo trim press.
Three-day event kicks off Oct. 24 in Cleveland.
Hybrids of additive manufacturing and CNC machining can shorten tooling turnaround times.
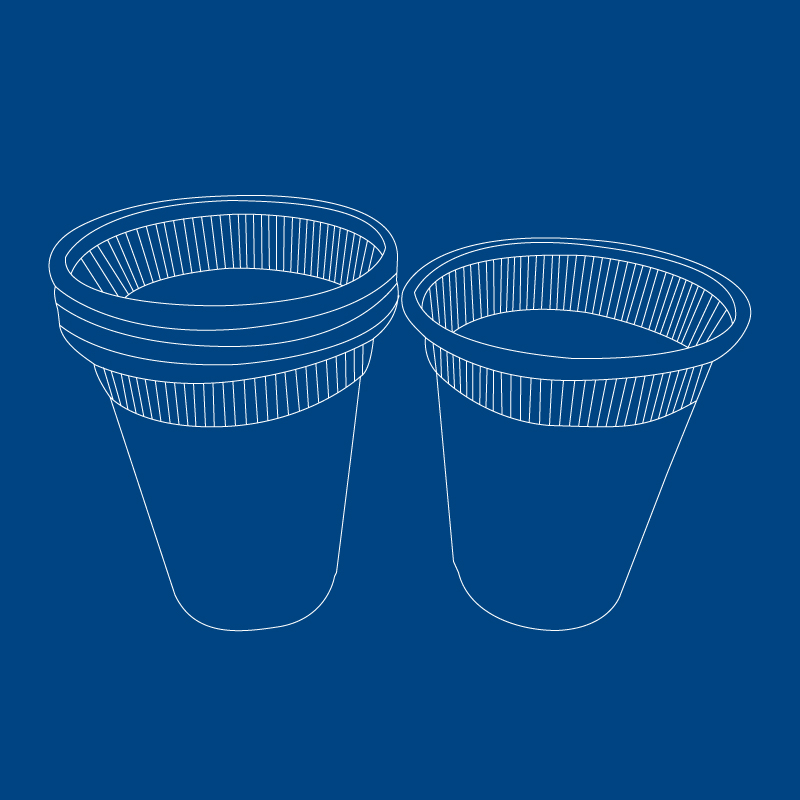
Thermoforming Machine © 2023 Gardner Business Media, Inc. Privacy Policy [Log On]