In wavelength-division-multiplexing (WDM) applications, several types of apparatus can combine multiple wavelengths of light for launch into a single optical fiber. These include arrayed waveguides, diffraction gratings, Bragg fibers, and multilayer bandpass filters (also called bandpasses). A particular technology may be selected based on its cost, physical size, insertion loss, and other factors. The multilayer bandpass filter is estimated to account for at least 50% of the world market in wavelength-division multiplexers or demultiplexers.
One example of a demultiplexer containing multilayer bandpasses separates signals into International Telecommunication Union (ITU) communication channels 31 through 36, spaced by 100 GHz (see Fig. 1). This separation translates to approximately 0.8 nm in the spectral region near 1552 nm. The center wavelengths of the individual bandpasses typically range from 1530 to 1565 nm. 4 Way Power Combiner
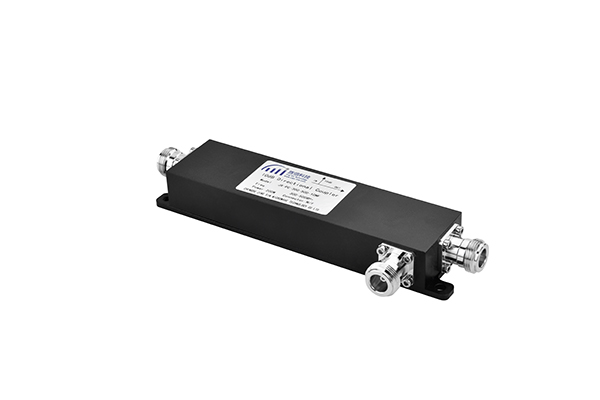
Demands upon the optical coating As early as 1995, the fiberoptic communications industry requested delivery of substantial numbers of WDM bandpasses. A typical specification for these devices is that the passband center wavelength should be located to a precision of ±0.1 nm and that the passband shift with temperature should not exceed 1.5 pm/K. It is no secret that from 1994 to 1996, many optical-coating companies attempted to produce these components. When the dust had settled a few years later, only three companies in the United States were shipping coatings in any reasonable quantity.
FIGURE 1. Schematic illustrates the use of all-dielectric multilayer bandpass filters for wavelength-division demultiplexing, including the input fiber and output fibers containing the demultiplexed signals (left). Omitted from the diagram are relay lenses that transfer the signal from fiber to fiber and filter to filter. Computed spectral transmittance of a bandpass filter that transmits International Telecommunication Union (ITU) channel 32 (dashed) is juxtaposed to one that transmits channel 31 (solid). Alternating dotted and shaded areas along the abscissa represent ITU communication channels 33 to 30. B is the bandwidth at the -0.5-dB level.
The reason so few firms succeeded is that coating standards for WDM are far more stringent than the standards the optical-coating industry was accustomed to. The coating industry had thrived for years on a standard of 1% control1% error in wavelength centering, 1% temperature shift, and so on. In contrast, bandpasses for WDM demanded a precision, not of one part in 100, but of one part in 10,000a factor of 100 times greater.
Furthermore, the number of layers in a WDM bandpass is considerably greater than for most other coatings. A typical laser gyro mirror, for example, contains 25 layers, and a sophisticated "hot" mirror 60 layers. The coating deposition time for the latter is seven hours. In contrast, the layer count of a WDM bandpass ranges from 100 to 200, and the time to produce these coatings often exceeds 50 hours. Mechanical stresses and the need for ultraprecise control of the layer thicknesses are just two of the problems encountered in the production of these coatings.
Equipment to produce WDM bandpasses Two pieces of equipment are sold in substantial quantities for bandpass coating production: the Leybold electron-beam evaporation system, and the Veeco/Ion Tech ion-beam sputtering system. A rule of thumb is that the equipment for the deposition of multilayer WDM bandpasses costs at least twice as much as a machine that produces conventional coatings.
The Leybold deposition machine evaporates alternate layers of silicon dioxide and tantala onto a planar glass disk that is rotating at high speed at the center of the evaporation chamber. The substrate temperature is controlled via a signal from a noncontact infrared thermometer. An ion gun bombards the substrate with argon and oxygen ions. It is this massive ion flux that produces films of high physical density. Because these dense layers are virtually impervious to water vapor, the resultant coating exhibits the required low temperature shift of the passband wavelength. An essential feature is the radiometric monitor (also called an optical monitor) and associated computer software that controls the layer thicknesses.
FIGURE 2. Five-cavity WDM bandpass has a -25-dB width of approximately 1 nm (left). The ordinate changes from linear to log at 0.9. The bandpass has a design that can be represented as: air 0.363L 0.260H 0.363L (L H)8 2L (H L)16 H L 3H 4L (H L)18 H 2L (H L)18 H 4L 3H L (H L)16 H 2L (H L)8 H glass, where H and L represent layers of optical thickness λ0/4 at λ0 of 1552.5 nm. The refractive indices of glass, H, and L are 1.50, 2.065, and 1.47, respectively. Note the nonquarter-wave thicknesses of the first few stacks. The optical thickness of the coating (in waves at 1552.5 nm) approaches 80 waves (below). The coating contains 184 layers; low-index layers are shown as green and red, while high-index layers are black.
The Veeco/Ion Tech coating system had its genesis some 30 years ago when ring-laser gyro mirrors were produced in large quantities in planetary fixtures. The WDM bandpass version abandoned the planetary for single rotation at the high speed of 20 Hz. A tunable laser radiation source and associated computer software control the layer thicknesses. The transmittance of the entire coating is measured as each layer is deposited.
By the spring of 2001, both of the aforementioned vendors were shipping hundreds of these deposition units annually. Many other vendors are also striving to produce equipment that will fabricate WDM bandpasses, and some are shipping units.
The bandpass that will be shipped The deposition of the coating upon the substrate is but the first step in the production procedure. The coating machine produces a bandpass filter on a circular disk of glass that ranges in diameter from 150 to 300 mm, depending upon the equipment. A typical disk thickness is 8 mm. Its uncoated side is ground to 1-mm thickness, optically polished, and then covered with a mutilayer antireflection coating.
Across the radial distance from the rotation center to the periphery of the disk, the center wavelength of the bandpass decreases. For example, in the Leybold system, from the disk center to the outside there is typically a 3-nm shift in wavelength. The disk is scanned spectrally and the annulus containing the "in-specification" bandpasses is located. These are then cut into 1.4-mm squares. Each filter must be individually scanned to ensure it is within specifications.
Design of the bandpass The bandpass consists of a quarter-wave stack of reflectors interdispersed between spacer layers of half-wave optical thickness, often called cavities. There are a few layers of nonquarter-wave thickness at the beginning or end of the stack. This five-cavity bandpass qualifies as a 100-GHz filter, because its full spectral bandwidth at the -25-dB transmittance level of 1.13 nm is less than 1.2 nm (see Fig. 2). The bandpass contains five spacer layers of both first and second order. In contrast to this five-cavity design, a four-cavity bandpass might contain 40 fewer layers and is, therefore, the preferred technology for 100-GHz bandpasses.
Figures reproduced from the book Optical Coating Technology with the permission of the author.
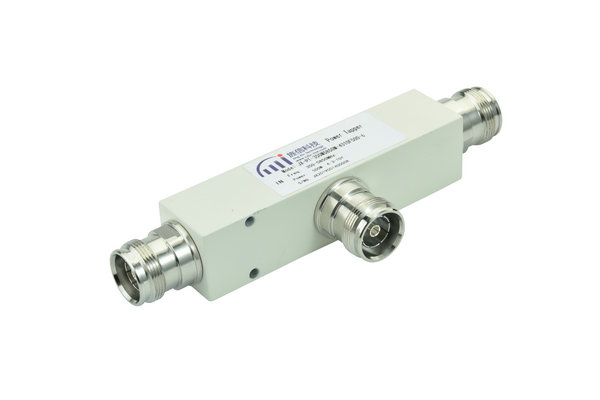
Waterproof Ip65 Cavity Filter PHILIP BAUMEISTER is a consultant at 1050 Sholem Lane, Sebastopol, CA 95472: e-mail: [email protected].