Home » Topics » Technology » 3 Ways To Reduce Downtime And Maintenance Costs With Video Monitoring
Video monitoring systems can help facility managers spot maintenance problems before they can develop into more costly issues. Wheel Bucket Sand Washer
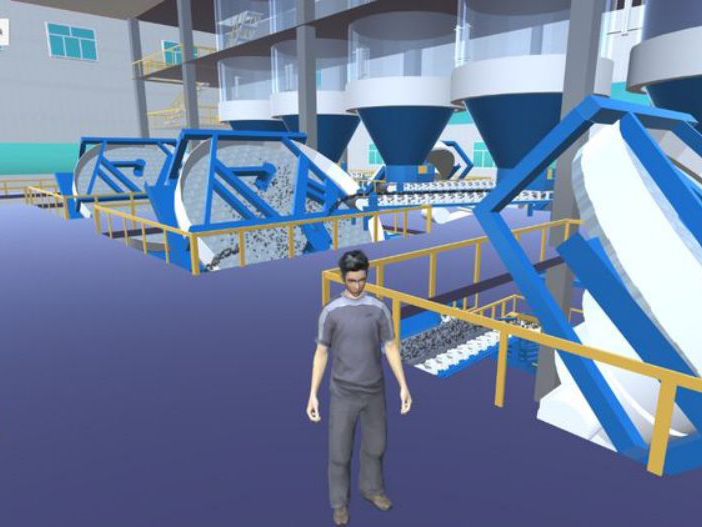
For manufacturing plants and other industrial facilities, maintenance and downtime costs are a big burden. The cost of downtime has gone up recently—it costs Fortune 500 companies 11% of their annual revenue, or $1.5 trillion, per a Siemens report.
Whether or not your facility is affected by mounting downtime costs, its undoubtedly affected by increasing maintenance costs. Optimizing maintenance costs leads to lower overall product cost and, therefore, to staying more competitive.
There are many ways to cut down on these costs, but one often overlooked one is with video monitoring systems. Video monitoring in industrial facilities can help you pinpoint proactive maintenance, catch issues before they cause downtime, and so much more.
Video monitoring for commercial and industrial facilities has come a long way in the past decade. You can find dedicated solutions for every application, including turnkey systems that support and enhance your operations. There are three key areas where video monitoring makes a difference:
While some downtime is perfectly normal in every facility, it’s the unplanned kind that wreaks havoc on your production and your revenue.
Unplanned downtime usually happens because of unforeseen incidents. For example, a conveyor belt can snap because it was nicked with a sharp tool or because of faulty joints. These seemingly tiny incidents can go unnoticed by employees that are actively working around the conveyor belt—they’re focused on production.
A remote operator with a video monitoring system, on the other hand, has a bird’s-eye-view. They can watch live feeds for the entire facility from one locale and spot small incidents before they turn into huge disasters.
When an operator spots such a problem, they can communicate with the floor operators to—in our example—stop the conveyor belt before it snaps. You can get it fixed quickly and get production back up and running.
You likely already have a facility maintenance schedule, but it probably doesn’t account for faster-than-expected wear and tear or fixing small issues before they shut down production. With a video monitoring system, constant surveillance allows for early detection of anomalies or irregularities that may indicate potential maintenance issues.
Video cameras provide visual data that can be used to inspect equipment and infrastructure for signs of wear and tear, corrosion, leaks, or other visible issues. This visual data can be valuable for detecting problems before they become critical.
By enabling predictive maintenance, video monitoring systems help facilities avoid costly unplanned downtime and extend the lifespan of equipment. This can result in significant cost savings in the long run.
Video monitoring systems enhance predictive maintenance by providing real-time visual data and enabling remote monitoring. They play a vital role in preventing equipment failures and optimizing maintenance schedules to improve the overall efficiency and reliability of facility operations.
As we’ve seen, video monitoring systems can play a significant role in optimizing maintenance work, which, in turn, leads to better productivity. They contribute to maintenance optimization and productivity improvement in many different ways:
This optimization leads to improved asset reliability, reduced downtime, and, ultimately, enhanced productivity for facilities.
You may already have a video monitoring system in your facility (and we’re not talking about security systems—those serve their own purposes). But is that video monitoring system helping you optimize operations and reduce downtime?
No two facilities have identical needs. More often than not, the environment dictates the type of cameras you need. In most cases, rugged cameras that are specifically designed for industrial environments are required—otherwise, you will be replacing them every couple of months.
Back to our conveyor example, if you want to monitor a belt on a piece of machinery that vibrates a lot, only certain cameras, can be mounted right on the equipment and handle the vibration and debris of being right on the line.
A high level of vibration, moisture, dust, splinters, grease—all of these will affect the way your cameras work and how often you need to replace them. Investing in the right type of cameras will lower your cost of ownership significantly. A good sign that your cameras aren’t right for the job are if they’re having to be replaced within 1-3 years.
When you’re installing or updating the video monitoring system in your facility, speak to a professional. Get their opinion on which cameras you should install and where. Make sure the cameras and other equipment can handle your environment so you can see the benefits of industrial video monitoring.
Schmidt has worked in the video technology space for almost 20 years, building expertise in CCTV, industrial video applications, new product development, video network solutions, and more. As a sales leader at Opticom Technologies, she helps customers implement robust video monitoring solutions for unique and harsh industrial environments.
Save my name, email, and website in this browser for the next time I comment.
Facility Executive is your one-stop source for information on quality operation, design and maintenance of facilities. Facility Executive offers a shared community of facility management experts who explore and analyze issues that affect your facility and its environment.
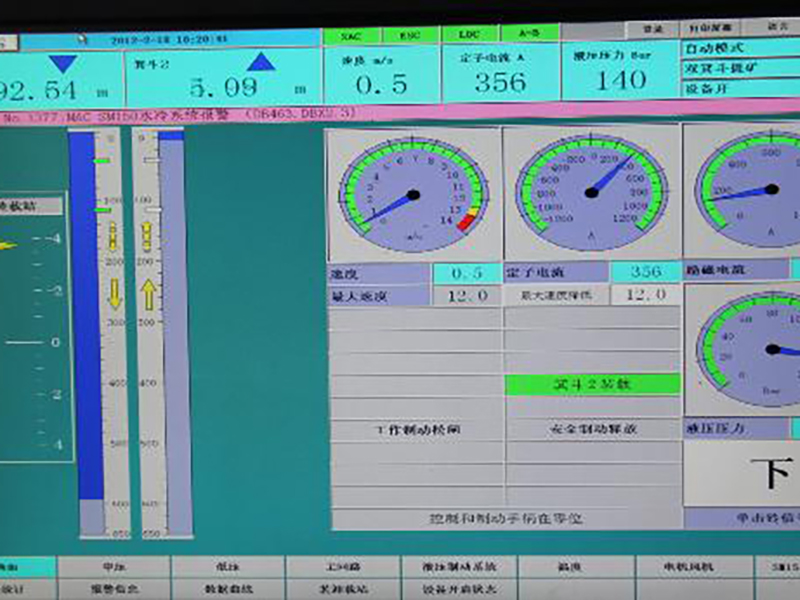
Pelletizing Expert System Facility Executive is a specialized trade publication written and edited for corporate facility executives in all industry and service sectors whose responsibilities include purchasing, planning and approving products, services and materials for facility operations.