In 2018, the first framework for adding automation to a frac stack was proposed internally. The proposal called for adding sensors and automated controls to hydraulic valves with a live data stream and post job analytics. Shortly thereafter, a novel third-party technology was identified and acquired. Pairing the service company’s operational expertise with the automation expertise of the third party, an expansive vision formed to methodically eliminate the primary barriers to fracturing the reservoir 24/7.
These barriers, identified as: 1) the time between stages (this includes transition time and pressure tests); 2) downtime associated with gate valve maintenance and failures; 3) pump maintenance; and 4) sand and water logistics, would be eliminated through novel, fit-for-purpose products, automated workflows and integrated control systems. Tilting Pressure Seal Cover Check Valve
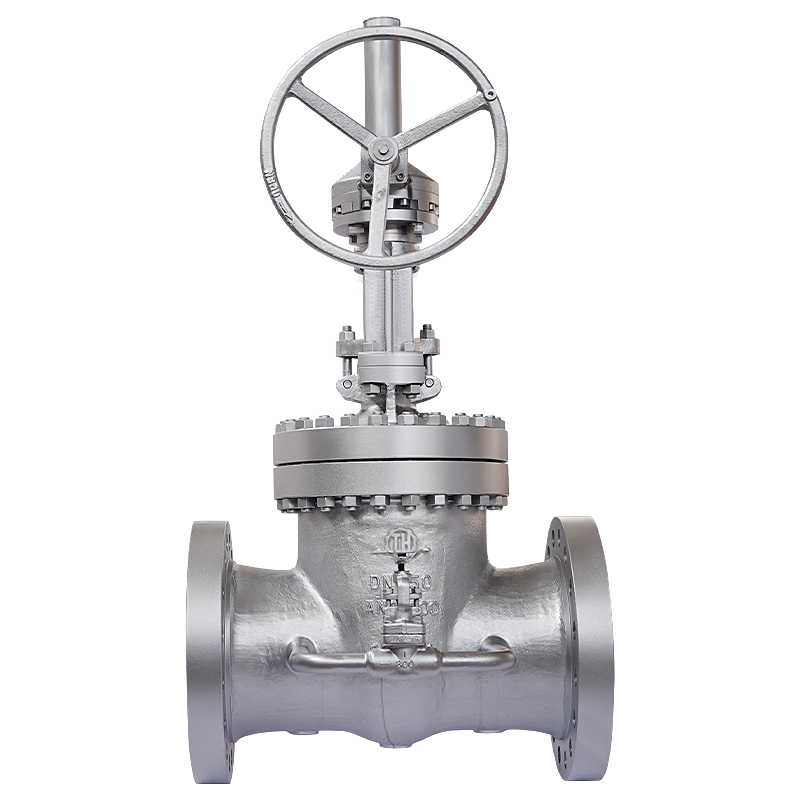
A roadmap was established that emphasized continual system development and increased levels of automation, as each hurdle was overcome, Fig. 1. Similar to the roadmap used for autonomous vehicles, the hydraulic fracturing roadmap utilizes successive improvements and integrations to functions and subsystems to achieve ever higher levels of autonomy, safety and consistency. Table 1 describes each automation level and its impact on safety, consistency and pump efficiency.
The surface system currently has been integrated into a single subsystem, achieving Level 4 automation. This subsystem is integrated into the wireline and pump subsystems, laying the foundation to achieve Level 5. Contrast this with most operators using Level 2 surface systems that employ multiple, non-integrated controls, leaving most process control to checklists, procedures, and human expertise.
Automated surface system (Freedom Series Completion System) to achieve 24/7. Several papers have been published regarding the automated surface system in its initial phases. The automated surface system has the following components, with several of the recent upgrades highlighted for further details:
These system components are integrated into a single, automated surface system that enables an operator to instantaneously transition from one stage to the next continuously, day after day. The system eliminates the four barriers to pumping 24/7 through the following means:
An automated lubricator reduces decision time, as well as potential NPT events:
Automated missile equalization. In many frac operations today, personnel enter the red zone to bleed off the missile. Integrated into the automated surface system is the bleed-down and equalization of the missile from the safety of the frac van, shortening the time required to switch out pumps and removing personnel from a hazardous red zone operation. This enables frac crews to always be completely red zone-free, eliminating the need for any exceptions. And it saves additional time and expense by automatically greasing the equalization plug valves, eliminating a potential source of NPT.
Automated pump swapping. The key remaining barrier is ensuring pumps are operational 24-hr/day to keep pumping at the prescribed rate. Today, the average frac crew utilizing zippers operates consistently at 16 hr/day, leaving a 50% upside in pumping each day when this problem is resolved. Figure 2 highlights the potential efficiency and utilization gains of employing the automated pump swapping technology.
The traditional approach to pump maintenance has focused on improvements to the pump truck. The automated pump swapping addition to the automated surface system approaches the problem differently by enabling a pump to be replaced without stopping operations or personnel entering the red zone. The system is placed between each frac pump and the missile. When a pump needs to be repaired or replaced, the system isolates the pump, bleeds down the pressure, and unlatches the pump. The pump truck is then removed out of the red zone to be repaired or replaced with another truck.
The repaired pump truck is backed into a set position, actuated arms couple the automated pump swapping skid with a hose plate mounted to the back of the truck, and the plates are clamped. A prime up-pressure test and equalization is performed before the pump is brought back online. Provided the benefits of the automated surface system, this additional technology enables an operator to achieve 24 hr of pumping per day. Benefits to the pumper include higher pump truck utilization, greater revenue, more frac jobs per month, and fewer trucks required on any given pad to maintain rate. A prototype was tested in July 2022, with eight pump swaps successfully completed without stopping the frac job, Figs. 3 and 4. Lessons learned from the prototype have been incorporated into the final product.
To achieve the goal of 24/7 fracturing required, a number of industry firsts are outlined below.
Self-equalizing automated valve. The base system, commercialized in 2019, automates the equalization process, enabling rapid transitions.
Remote, integrated latch. Part of the base system, the integrated latch is interlocked with the automated valve, eliminating potential pressure releases by ensuring the latch is properly tested and in place before the valve can actuate. In addition, the system allows the lubricator to be attached during frac, eliminating time on critical path for this task.
Digital handshake. A unique authentication code, changing every 30 sec, is tied to each person authorized to use the system. The digital handshake reduces the risk of NPT by ensuring the system is operated only by qualified personnel and provides traceability, if issues occur.
Remote hydraulic greasing. Other greasing systems traditionally use pneumatics to drive grease. Using hydraulics delivers a pressure curve, providing assurance of grease, eliminating greasing time as well as reducing valve-related NPT events.
Integration of the surface system. Traditional surface systems have multiple, non-integrated controls. For illustration, the typical surface system has separate controls for each valve, the greasing system, and the latch system. Process control is achieved through human-driven workflows, checklists, placards, lock-out/tag-out. Human-driven workflows are prone to error and, therefore, NPT. The Freedom Series completion system fully automates these sub-systems into an integrated system.
Continuous pumping well transitions. The first continuous pumping transition was conducted in October 2020, in the northeastern U.S. Continuous pumping is a process that reduces stage-to-stage transition time to seconds.
24-hr continuous pumping. This milestone was first achieved in September 2021 and represents the initial step toward continuous pumping 24/7.
Remote frac plan execution. The ability to execute the next well transition from a remote frac plan entered by the completion engineer, providing frac flexibility to the engineer, as well as ensuring the correct stage is completed. The system maintains a queue of fractured wells and will work through prescribed steps suggesting swaps in order of wireline activity or will pull from a stage list provided by a completion engineer. Either way, it will then remove the well from the available wells to frac until it sees wireline activity again. It eliminates the human decision factor when swapping, providing the ability to auto-swap as we progress to Level 5 automation.
Swapping a pump while treating. Demonstrated in July 2022.
Automated simulfrac transitions. In May 2022, the automated surface system was adapted to simulfrac operations, eliminating stage-to-stage time on simulfrac jobs.
Continuous pumping on a simulfrac job. In May 2022, the automated surface system transitioned from two wells to two separate wells, performing 11 valve actuations, and initiating greasing of each valve, all in under 40 sec, facilitating the opportunity to pump 24/7 on simulfrac operations.
The age-old debate that is generated when a new technology stands to replace current practice is well-documented. This same debate can be heard today within the frac community, relative to surface system automation. Historically, OFS has done manually what Downing (an SEF Energy company) does automatically (but have you done it every time), we need to work on all our issues before we take on a new system (SEF’s system removes many problems, so you can focus on other issues), our pumps cannot keep up, we have sand and water issues.
What is lost in the debate is that each issue masks another. If you have pump issues, this may be masking valve issues; supply issues may be masking pump issues. In addition, without the high-resolution data available, determining the root cause of an issue is often difficult and sometimes impossible. Process improvement involves systematically, eliminating an issue, and then focusing on the next issue to be resolved. Referring to the roadmap in Fig. 1, Level 0 to Level 3 automation involves human interaction between functions, requiring time-consuming processes, checklists, and personnel expertise. As noted, when issues inevitably occur, it is difficult to find the root cause with the disparate systems on pad.
As personnel change over time, process discipline and experience are lost, leading operators to again experience issues they thought they had resolved. Automated workflows found in Levels 4 and 5 are driven by one second of data capturing every system function. System data and automated workflows reduce non-productive time in two ways: 1) through real time alerts warning the operator of impending issues that need resolution; and 2) NPT-causing issues that occur are positively identified through root cause analysis and, unique to automation are engineered and/or programmed out, permanently eliminating that issue.
Figure 5 illustrates why automation is key to permanently eliminating issues. With the passage of time, the system becomes more robust, leading to faster and more consistent frac jobs. To illustrate this concept, the system initially used wellbore fluid to equalize through a ball valve and choke. Sand in the fluid caused wear on the ball valve. In addition, the choke had to be properly sized, based on well parameters. Identifying this as an opportunity for improvement, the ball valve was engineered out of the system, replaced by a boost pump and clean fluid to perform equalization and fill the lubricator.
The automated surface system generates gigabytes of data per job, tracking everything from pressures to valve positions, to open and close events. These data are used in real time for
lockouts, ensuring the system only operates when the prescribed conditions are present. In addition, the data are used for live and post-well analytics to improve operator performance. The data are also used for failure mode analysis, leading to new signatures for alerts identifying potential NPT. A few of the data applications are highlighted below.
Operational dashboard. Unique to the automated surface system, an operational dashboard (Fig. 6) provides the interface for the operator, onsite service personnel, and remote operations personnel to maintain the surface system, preventing NPT events prior to occurrence, as well as identifying improvement opportunities in real time. The dashboard trends operational data, provides real-time status of all systems, alerts personnel of both potential failures, as well as predictive maintenance events, and provides insight for operational improvements.
An adaptive grease algorithm (AGA) has been added recently to the automated surface system. The AGA was developed to ensure all gate valves are greased properly upon every actuation (defined as packing off the grease void with grease and then stopping), reducing grease and valve repair costs and eliminating premature valve failures. This both ensures the grease void is full for every actuation while also eliminating excess grease and subsequent issues associated with grease in the borehole.
Initial deployment occurred in October 2022 with striking results, Table 2. Pump strokes (correlated to the amount of grease consumed) to grease each zipper, pump down and stack valve were measured before and after implementation of the AGA. Overall, grease volume decreased by 55% across all valves (see adjacent table), with no detrimental effects to valve repairs or NPT. Subsequent application of the AGA has seen grease volume decrease by up to 90%.
Latch-to-latch (L2L) is calculated and plotted as a measure of wireline turnaround time, from the time of unlatching the wireline to when it is stabbed and latched again, Fig. 7. In addition to L2L, fill and drain times are also captured to the second.
Stage-to-Stage (S2S) time is defined at two locations: 1) the time between stages at a prescribed pressure (just under treatment pressure) and 2) at treatment pressure, Fig. 8. Stage-to-stage captures the white space between stages, consisting primarily of transition time, pressure test time, non-pump maintenance time, and ramp up/down of pressure and pump maintenance time. It also includes non-productive pumping (NPP) time, defined as time after a transition but before the frac is back at treatment pressure, not captured in traditional pump efficiency calculations. NPP includes time to ramp up pressure, pressure tests and spotting acid on critical path.
Stage-to-stage is a better indicator of job efficiency than pump efficiency. Pump efficiency suffers from several flaws that make it difficult to compare one job to another including the following:
Long vs short stages. Long stages artificially inflate pump efficiency. Comparing two frac jobs, one with long stages (e.g. 3 hr) the other with short stages (e.g. 1 hr), the longer stage job could be deemed more efficient, due to the operational cost of transitions on the shorter stages. This can give the false impression that one crew is better than another. As a side note, significantly reducing the operational cost of the transition with the automated surface system, provides completion engineers more flexibility when designing their treatment program (i.e. providing additional options for limited entry fracs through shorter stages).
Defined calculation. Pump efficiency is not captured in a consistent way from operator to operator or from pressure pumper to pressure pumper. This leads to errors comparing different crews, operators, or pressure pumpers.
Includes NPP (Non-Protective Pumping). Pump time is often started after the transition but before the pumper is back at treatment pressure. Recalling the goal to pump 24/7 at treatment pressure, transitioning is only one part of the time between stages. As noted above, the time between stages can also include NPP, slow ramp up times, and waiting. Not only does this provide a false measure of efficiency, but when charged by the pump hr, a job will cost more.
To compare the efficiency of one job to another, the S2S is plotted on a histogram ranging from 0.5 minutes (min.) to 60 min. between stages, Fig. 9. Stage-to-stage is plotted as a percentage of the total number of stages. For example, using Fig. 9, 28% in the 0.5-min. range signifies 28% of the stages were transitioned in less than 30 sec, representing continuous pumping operations (continuous pumping typically is in the 30-60 sec range). The 60-min. bucket was chosen as a cutoff, given anything over 60 min. indicates serious problems on the pad that can span days, unnecessarily skewing the S2S. This also is an indicator of the quality of a job, as a low percentage in the 60-min. bucket (<90%) indicates more problems than the typical pad.
Figure 10 highlights S2S plotted as an overall average time, with a 95% confidence interval showcasing transition consistency throughout the job. As noted, S2S over 60 min. has been removed, as larger issues, some lasting days, can skew what would otherwise be an excellent job.
Although not a universal practice, many operators utilize ISIP to gauge the quality of each frac stage. Traditionally, this requires a well to be shut-in for a set period. An engineer selects several points on a screen to establish an ISIP number. There are several issues with this practice including: 1) requires up to 5 min. between stages in which operation is shut down; 2) requires time for an engineer to collect and then manually pick points on a pressure curve; and 3) can be inconsistent, based on the level of experience of the person calculating the ISIP.
The operator requested this process be automated from surface system data. They recognized that by utilizing the automated surface system, the ISIP could be calculated without operational or administrative cost. The system is open to each well the entire job, eliminating the need to stay on a specific well for minutes after the end of the stage waiting for the data to be captured. In addition, the lengthy ISIP data process includes downloading the data, plotting the data, and manually capturing the ISIP. This process was automated and is performed in real time by the automated surface system’s edge computers on the specific well, utilizing derivatives to capture ISIP. The ISIP is then streamed to the cloud, where the engineer can download the specific number for each stage.
To validate the results, an experienced engineer captured the ISIP data manually, using the “Superior ISIP” method and compared it to both the ISIP derived from the automated surface system as well as that supplied by the pumping company. Figure 11 highlights that the system-derived ISIP from the automated surface system and the superior ISIP match almost exactly, establishing the accuracy of the automated surface system ISIP calculation. The yellow ISIP points (collected from the pressure pumper) are obviously flawed by continuous pumping operations but also inherent inconsistencies of data collection at the human level.
Blue Ox Resources, a private equity-backed Permian Delaware company based in Dallas, Texas, chose to employ the automated surface system after utilizing it with their former company, Primexx. Primexx was an early adopter of the automated surface system and has contributed insights to its development over the past three years. The system was chosen for its efficiency, the elimination of human error, interlocks that prevent deadheading or cutting wireline, and the inherent safety of the system through the removal of people from the red zone and the pad. With their previous experience, and employing the latest additions to the automated surface system, Blue Ox Resources set new efficiency records with the system on the El Duderino East and El Duderino West pads, Fig. 12.
Located just south of Pecos, Texas, both El Duderino pads (Fig. 13) consisted of 3 wells each, spaced 200 ft apart, Fig. 14. The east pad comprised 130 total stages, with the west pad at 126 stages. Pump times averaged 110 min./stage (at treatment pressure), and 100 mesh sand was used. The stack configuration (manual valve, hydraulic valve, cross, with the base system on top of the cross) is 15k-rated. The zipper consists of two hydraulic valves, which are both actuated during the transition, providing a constant double barrier. The pressure pumper provided 22 Tier II pumps with 2007/2008 manufacturing dates.
To maintain rate, 16 pumps were required at any one time. The pressure pumper contract does not include any mandatory maintenance periods. The pressure pumper does have internal personnel incentives to pump more hr/day. The pressure pumper runs until they are down to 16 pumps, completing the stage they are on before shutdown. The operator then shuts down the pad, the non-operational pumps are repaired, and preventative maintenance is done on the other pumps. As soon as 18 to 20 pumps are ready, the frac job resumes.
Prior to the job, Blue Ox Resources required the surface system provider, wireline and pressure pumper representatives, along with the field operators, to meet to fully understand the automated surface system and how it operates. Expectations were set by Blue Ox Resources that at least 10 stages would be pumped each day, and continuous pumping would be done on every stage possible.
Utilizing the stage-to-stage times to accurately judge the performance, the Blue Ox Resources jobs were compared to the previous 15k record in the Delaware basin, Fig. 15. In September 2021, the first job to continually pump for 24 hr was recorded (with subsequent records set on the same pad at 35 hr), with the average S2S time for the job at 10 min., continuously pumping 50% of the stages.
In the same year, Operator 1’s Nimitz pad dropped the S2S average to 9.2 min. The average S2S for Operator 2’s two pads was lowered to 5.4 min. and 3.3 min, respectively, in December 2022, continuously pumping 70% of the stages. The 95% confidence interval also tightened with the latest Operator 2 jobs, documenting the consistency of the S2S. A job continuously pumped 24/7 would show 100% in the upper left-hand corner of Fig. 12. Both jobs pumped over 10.6 stages per day, with the El Duderino East achieving 10.7 stages per day.
As noted above, the first version of the automated pump swapping system was tested in July 2022, with the test validating the coupling/decoupling sequences. Lessons learned from the first iteration were applied to the second prototype including:
The revised system was tested in late January 2022 on Operator 2’s Gutterballs State 14-15 pad. The system under test utilized a missile automation skid connected to the missile (automates the functionality of any missile) and two automated pump swapping skids each connected to a frac pump on one side and the missile on the other through the missile automation skid, Fig. 16.
Each frac pump was modified with a simple plate on the back of the truck mounted at a set location. This plate contains two subs for the pump’s high-pressure and low-pressure lines connected to the frac pump, Fig. 18. Adapted to any frac pump, this enables a frac pump of one manufacturer to be swapped with a frac pump from a second manufacturer. With each pump backed into the skid, a coupling sequence is run, securing the frac pump to the automated pump swapping skid. The suction and discharge valves are then opened, allowing the frac crew to run their normal pressure test routine on the initial rig-up, prior to the start of the frac job. The coupled pump and automated pump swapping skid can be seen in Fig. 17.
Multiple coupling and decoupling sequences were run with the pumps offline to verify the coupling sequences. Automated pump swapping while continuing to frac was then tested. This involved isolating the pump requiring repair, bleeding down the pump, and decoupling while the remaining pumps continue to frac. The pumps were then repaired outside the red zone, pulled back into the automated pump swapping skid, coupled, primed, pressure-tested, and equalized (suction and discharge lines are opened), bringing the pump back online while the remaining pumps continued to pump. This was done four times, with each test more rigorous than the prior test. Results of the four tests are shown in Table 3.
The two key lessons learned from the first iteration, making the system agnostic to the pump and missile, and isolating the pump vibration, were successfully integrated into the second version of the system. The system worked as intended and is being integrated into the automated surface system. The new automated pump swapping system is now in production and will be deployed as an integral part of the automated surface system.
An automated surface system, the Freedom Series Completion System, has been developed to systematically eliminate the primary barriers to fracturing the reservoir 24/7. With the integration of the frac and wireline systems into the automated surface system, the system has successfully pumped continuously for multiple days on multiple pads. The final hurdle to 24/7 fracturing was to eliminate pump maintenance as a barrier. With the advent of automated pump swapping, this barrier has been eliminated. The system is now in place to achieve continuous 24/7 fracturing operations and with ongoing development, the automated surface system is nearing Level 5 automation.

Rsv Gate Valve The authors would like to thank ProFrac for their help testing the second iteration of the automated pump swapping system. Also, thanks go to Liberty Energy and Steward Energy for their help testing the first iteration of the system. This article contains excerpts from SPE paper 213101-MS, “Automated completion surface system: The path to fracturing 24/7,” presented at the SPE Oklahoma City Oil and Gas Symposium, held at the Oklahoma City Convention Center, April 17-19, 2023.