SII Dry Kilns Supplies More Drying Capacity to Meet Growth of Bingaman & Son Lumber
KREAMER, Pennsylvania – Bingaman & Son Lumber produces lumber products from the hardwoods of the Appalachian Mountains region. It puts a premium on lumber quality because the lumber is supplied to businesses that use them to manufacture high value wood products – products that are valued at least in part because of their wood color and quality. SW Hf Wood Drying Plants Exporter
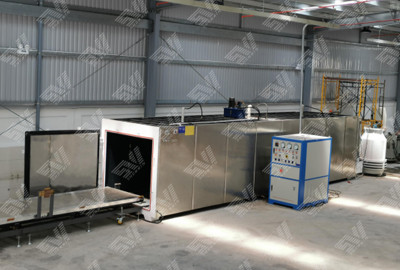
For about the past 10 years or so, Bingaman & Son has turned to SII Dry Kilns when it comes time to add kiln capacity and to ensure its drying operations will produce high quality lumber.
Ironically, their bond between the two companies was forged when SII personnel helped Bingaman & Son when it was dealing with a lumber thermal modification system that didn’t work properly – a system supplied by a different business. “It was because of the approach they took in terms of the way they supported us,” said Chris Bingaman, president and CEO of Bingaman & Son. “It’s been a lot of cooperation back and forth on thermal modification and the dry kilns.”
Carson Bingaman operated a general store and began selling hardwood lumber to shore up coal mines in the 1930s. Today the company is led by Chris, 65, whose father Max, 87, still comes into the office most afternoons. “Quite a few” family members are involved in the business, including three nephews, a son-in-law, and uncle.
Bingaman & Son has five locations, all in Pennsylvania. Its headquarters and value-added operations are located in Kreamer, which is located pretty much in the center of the state, some 50-miles north of Harrisburg. Other drying, surfacing and export operations are located in Clarendon. The company also acquired three sawmills – two since 2006 – that operate as affiliated business units in Mill Hall, St Marys, and Nicktown. The company’s operations currently employ some 225 people; the workers own a 35 percent interest in the business through an employee stock ownership plan.
The three sawmills supply about 14 percent of the company’s lumber. Bingaman & Son buys additional green lumber from 145 mills in the Appalachian Region states of Pennsylvania, New York, Ohio, West Virginia, Virginia, and Maryland. Virtually all – 99 percent – of the company’s production is hardwood.
The three mills are profit centers, not cost centers, explained Scott Shaffer, vice president of yard operations, and the two concentration yards operate as their own profit centers, buying lumber from elsewhere as needed. “That’s a unique way of doing it in the lumber industry, in my opinion,” said Scott.
SII Dry Kilns has supplied seven conventional lumber kilns for Bingaman & Son Lumber, including three that began operating in the summer of 2022. The kilns feature all SII components and controls.
Company foresters buy timber, and Bingaman & Son uses contractors to harvest the trees. Grade logs are delivered to the Bingaman & Son mills, low-grade logs and pulp are supplied to other mills.
Bingaman & Son Lumber sells everything from logs to value-added lumber products. About 50 percent of sales are lumber, 40-50 percent are some type of value-added product, and logs make up the remainder. Approximately 25 percent of its production is for export markets.
Bingaman & Son is very diverse, noted Chris. The company sells to a wide range of direct users and has customers around the globe. “We really work at diversity in two ways, products and species.” With its mills located in the heart of the Appalachian hardwoods region, the company has access to various species of maple, oak, cherry, birch, poplar, and others. In addition, it provides value-added services for customers. Those include surfacing, ripping one edge or two edges, chopping, finger-jointing, and thermal modification. “We can support customers who want different options,” said Chris, “as they adapt to different fashion trends. We can get a customer the most refined product they need.”
The company sells mainly to the wood manufacturing industry – think manufacturers of furniture, cabinets, and other wood products. “That’s who we’re there to support,” said Chris. To cite just one example of its value-added products, the company makes glued blocks that are used in windows for commercial buildings.
“Our goal is to work with the wood manufacturing industry,” said Chris, “to help them get what they need from the resource that we have and to minimize through-put. There are a lot of variables in the wood market. We’re trying to take those out and give the manufacturers what they want. We use our diversity to do that.”
Of course, lumber drying is a key component of the company’s operations, particularly for value-added products. In all, 80 percent of the company’s lumber products are kiln-dried. Of the kiln-dried products, about half is rough lumber and the other half is destined to be processed into some value-added product.
Ed Greene of SII inspects a load of ash lumber that was thermally modified in a WDE Maspell thermal modification system. Bingaman & Son has three of the systems. SII represents WDE Maspell, an Italian company.
Bingaman & Son has 20 lumber kilns in all, 14 at its Kreamer facilities and the other six at Clarendon. The kilns have a combined drying capacity of 1.2 million board feet. The company also has a pre-dryer with a capacity of 520,000 board feet.
Seven conventional kilns have been supplied by SII, including three that began operating in the summer of 2022. Each of the new kilns has a capacity of 50,000 board feet. They feature all SII components and controls. The company has a wood boiler and a gas boiler to supply heat to the kilns.
The latest kilns from SII feature SII’s ‘Kiln Dry’ software, which allows for semi-automatic control around the clock. They also feature SII’s power venting system, which enables maximum venting when drying species like hard maple and poplar, which dry faster. The kiln doors open and close with hydraulic door carriers, allowing for one person operation.
“These kilns were constructed in the place of some older kilns, and we had to utilize existing control rooms on the rear wall of all five of the newest kilns,” said SII’s Dan Mathews.
“It was tricky,” said Scott Shaffer, vice president of yard operations for Bingaman & Son, “but they were able to pull it off.”
The kilns have a cool section and hot section in the control room. “We feel that’s a decision that creates more longevity with the a/c drives and your equipment,” said Scott.
The fan motors are regulated by individual variable frequency drives to control fan speed. As with all SII kilns, roof panels are made of 304 stainless steel.
SII Dry Kilns is a family-owned and operated business located in Lexington, North Carolina. The company designs and manufactures kilns for drying both hardwood and softwood lumber. For the hardwood industry it offers two types of kilns, conventional front-end loaded with overhead fans and heat and a larger capacity ‘SII “Design’ that loads from both sides of a center fan wall. For softwood lumber drying SII offers batch track kilns and (CDK) dual path continuous dry kilns. SII also offers its own kiln control systems and software. It also manufactures pallet heat-treating systems and kilns for drying firewood, walnut steamers, fan sheds, and pre-dryers. SII has over 2,000 kilns in operation worldwide.
Bingaman & Son Lumber sells everything from logs to value-added lumber products – virtually all of it Appalachian hardwoods. About 80 percent of its production is kiln-dried. The company sells mainly to the wood manufacturing industry – makers of furniture, cabinets, and other products.
(For more information about SII Dry Kilns, visit www.siidrykilns.com.)
Bingaman & Son has been “very happy” particularly with the SII kiln controls and venting system, said Chris. “Some of the features of SII kilns have been very good for meeting lumber quality.”
“We love partnering with SII,” said Scott. “They’re a really well-run company. They’re self-aware. They know what they can do and what they can’t do. They’re consistent. When they say it’s going to be up and running, it is. And they’re a company of integrity,” which is one of the core values of Bingaman & Son.
The business relationship between Bingaman & Son and SII Dry Kilns had an unusual genesis. The leaders of the two companies had some contact with each other over the years, making connections at trade shows and other interactions. Bingaman & Son became interested in thermal modification of lumber, and it considered investing in a Russian-made system. Dan was interested and met with Chris to learn more about the technology. “I appreciated his assessment,” said Chris. “I learned a lot from the SII team.”
Thermal modification of lumber is akin to baking it. The wood is heated to 400 degrees (F), a temperature that eliminates the living matter and changes the structure of the wood.
Once treated, the lumber can be used for exterior applications because it resists moisture and requires no chemical additives to protect the wood. The treatment process was developed and is used extensively in Europe.
Bingaman & Son invested in the Russian-made system, but it failed. Dan reached out to the company to offer SII consulting services to aid them. “Just the way they serviced us…their whole attitude gave me a whole lot of respect for SII’s approach,” recalled Chris. The company began to consider SII as it sought to add kilns.
Chris cited the support they have received from SII and the trust in SII leadership. “They’re very transparent with what they know and don’t know,” said Chris. “When it comes to the dry kilns, everything they’ve told us was borne out – delivery dates and so on. And they gave us good advice about removing some old kilns. They’ve been a very reliable partner and supporter of our drying operations and thermal modification.”
Bingaman & Son eventually invested in three thermal modification systems from WDE Maspell, an Italian company. In another twist, WDE Maspell was seeking an American company to represent them in the U.S., and Chris introduced them to Dan and SII, and now SII represents the Italian supplier. “It’s been a lot of cooperation back and forth,” recalled Chris between Bingaman & Son and SII Dry Kilns in the realms of thermal modification and lumber kilns.
The company’s thermal modification systems can process 40,000 board feet per week. Thermal modified lumber products account for less than 10 percent of revenues at this time. However, Chris is optimistic.
“It’s a developing market,” he noted. Thermally treated wood is an alternative to tropical wood species and non-wood alternative materials. “We’re trying to get into distributors for decking material, outdoor furniture manufacturers, and other potential users. We’ve done some projects for boardwalks.”
“We believe interest will continue to grow in North America,” added Chris.
Market conditions have been very challenging since mid-2022, acknowledged Chris. The pandemic spurred strong demand for lumber as homebound consumers increased spending on renovations and home improvement projects. Lumber prices escalated. However, export markets have slowed in Europe and China, and now the domestic market is softer. The result is an abundant supply of lumber while prices have dropped rapidly.
It’s a “painful process,” said Chris. However, the industry is adjusting. “We’re getting closer to an alignment of supply and demand.”
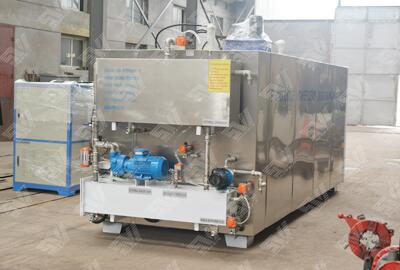
SW Hf Wood Drying Room Factory Bingaman & Son unashamedly embraces Christian values. As the company’s website notes, the business was founded – like others – to make a profit. “Undoubtedly, it is the deep conviction of company owners that we must have an even greater objective that is far more important than any other; that being to glorify God in what we are doing. Certainly God’s word to man is very clear, that whatever man does is to be done for God’s glory.”