A project between Callidus Welding Solutions and Deakin University researchers has resulted in seated ball valves with superior durability, according to the participants.
Such valves are crucial in hydrometallurgy production of critical minerals such as nickel and gold, and according to the Innovative Manufacturing CRC – which sponsored the project – can cost upwards of $250,000 each. Stainless Ball Valve
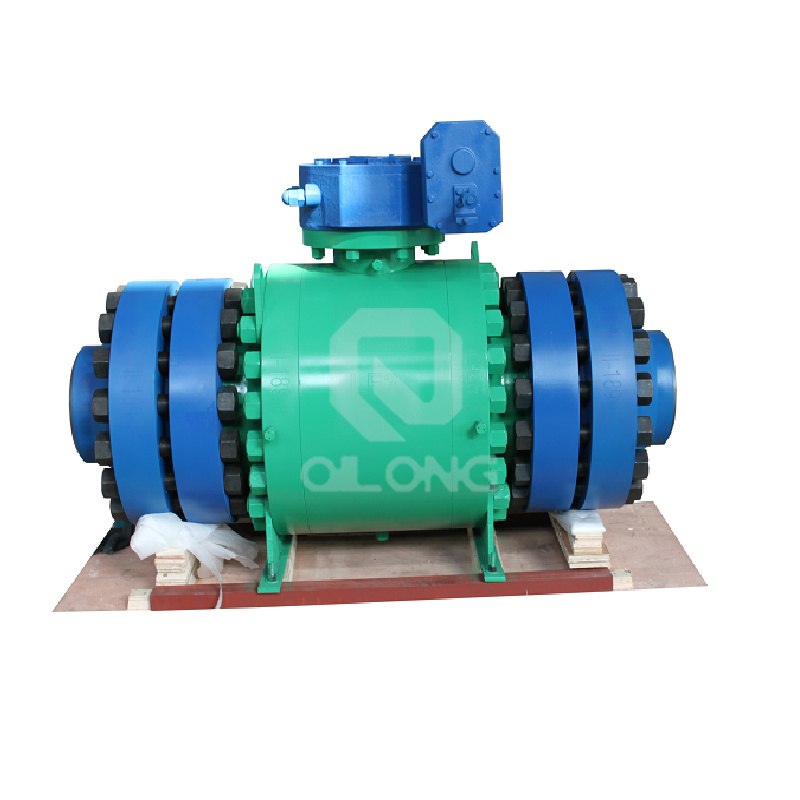
The IMCRC awarded the project an $85,000 grant through its activate program, aimed at shorter-duration, high-impact projects. It delivered a new system with superior fusion of ceramic coatings onto the metal surface of valves. The total project was budgeted at $585,000.
“The outcomes of the collaboration have broadened our application base and product portfolio, allowing CWS and our parent company Callidus Process Solutions to provide a real-world commercial solution to premature valve failure,” said the project’s leader, Joe Ellis, Automation Supervisor at CWS, in a statement on Tuesday.
Dan Fabijanic, an Associate Professor of Metallurgy at Deakin University’s Institue for Frontier Materials, said, “This collaboration has allowed Deakin’s metallurgy and materials researchers to effectively integrate with industry and deliver a product of significant benefit to CWS’ customers.

Socket Weld Ball Valve “By bringing together Deakin’s research expertise and CWS’ industry insights, IMCRC’s collaborative model has enabled us to share learnings and more quickly iterate to not only find a solution to this challenge but to explore new R&D avenues.”