Built Robotics provided Bechtel with controls that allow for excavators to be run autonomously, supervised by an on-site operator in a nearby trailer. Photo courtesy of Built Robotics
As equipment manufacturers further embrace electrification and autonomous operation, positioning, middleware and robotics technology providers such as Moog Construction, Built Robotics and Trimble are looking to help contractors test the waters of the future. Open-pit Mining
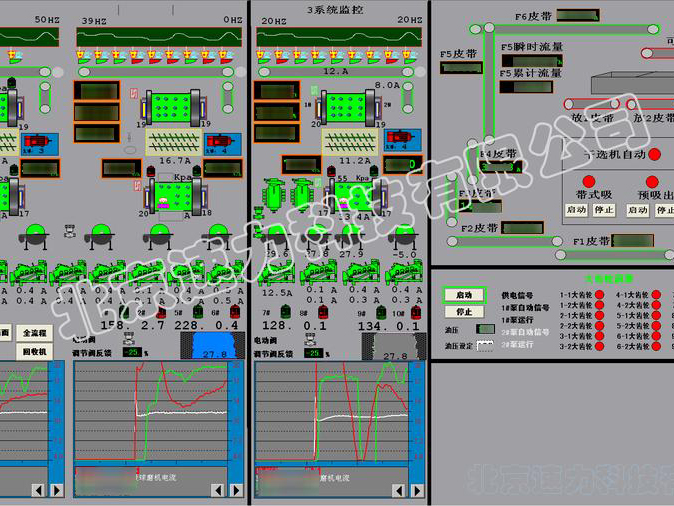
Switching to electric or autonomous operations is no small expense for contractors. Costs vary, but a battery-powered piece of heavy equipment can have a premium of 50% or more over diesel machines, and that’s before factoring in prices to install charging stations and update service bays.
Aftermarket electrification of diesel-powered equipment can get contractors acclimated to these new systems for a lower price, while dealer-installed sensor packages offer a taste of semi-autonomous machines. Rental channels are another way to try out these new ways of working.
SunBelt Rental took the first 100 units of the all-electric Bobcat T7X compact track loader in 2022, and extended that deal with additional units purchased earlier this year. The T7X has Moog’s integrated software framework, an electric machine controller, lift and tilt electric actuators, electric traction motors, and the formerly diesel engine compartment is filled with batteries and electronic controllers. Its lift runs on electric-powered actuators, not hydraulics, so while it has the power of a regular Bobcat T76 track loader, the battery and controller components makes the T7X about 1,000 lbs heavier, resulting in some different handling for the operator.
The autonomous compact track loader (above) can be programmed to deliver materials or perform other tasks by a remote operator using Moog’s software (left). Photos by Jeff Yoders/ENR
Bechtel Chief Innovation Officer Keith Churchill and Ken Burke, the firm’s global operations manager, worked at the company’s Houston-area equipment yard in 2021 using hardware from Built that allowed the firm’s excavators to be run fully autonomously.
Churchill said a competitive labor market made it advantageous for the major EPC contractor’s skilled operators to oversee several of the autonomous excavators from a trailer rather than spend hours at a time digging trenches for large solar farm projects in Texas and Louisiana.
Operators could monitor the Komatsu and Caterpillar excavators on site as they dug ditches for electrical lines and holes for piles to support the panels. Built’s system was tested by Burke and his team at Bechtel’s yard, and they came up with improvements such as using a safety geofence to make sure the excavators automatically shut down if they got too close to humans. Built’s system fits onto regular Caterpillar and Komatsu hydraulic excavators, turning the machine’s electrohydraulic controls over to an onboard computer programmed to perform standardized and repetitive excavation tasks as loaded prior to operation. On Bechtel’s solar projects, Built-enabled excavators achieved a 93% uptime at a productivity rate of 191 linear ft per hour—a 45% productivity increase over a single operator digging trenches.
Moog’s autonomous, all-electric track loaders are seeing similar duty on a major solar energy provider’s utility-scale solar project in western New York. Each loader has a GPS unit as well as front and back-mounted cameras and LiDAR sensors that communicate directly with Moog software. This setup allows an operator to program simple commands, such as to pick up pallets of materials in a lay-down area and deliver them to where they’re needed, then turn around and repeat the task.
The autonomous track loaders are delivering materials such as polysilicon photovoltaic panels, which each weigh 80 lb. The project site, like most utility-scale solar, is in a remote area, and installation crews require delivery of hundreds of pallets of panels every week. Moog business development manager Aditya Sharma said autonomous delivery function brings a level of consistency the contractor needs.
He said Moog’s roots in the kind of mechatronics already widely applied in space exploration, military applications and oil and gas exploration is an advantage for company partners such as Bobcat and Sunbelt when it comes to both autonomy and electric operation.
“A lot of the [construction] OEMs don’t have the engineering team or the actuators, the servo motors to put this together. So they’re out trying to source it from all different points on the compass,” explains Thomas Greier, systems engineer for robotics at Moog. Greier says the company’s current focus on solar is a function of those projects being labor intensive, dirty, remote and in high-demand in the ongoing transition to clean energy generation. Greier also believes that, once operators understand what they can do with electric machines, they’ll come to prefer them to diesel equipment.
“Your power is distributed. So, unlike a traditional hydraulics system, you have independent horsepower at each axis; you can do full power and lift and tilt and traction, all at the same time, depending on your application,” says Erik Berg, senior systems engineer at Moog Construction. “This is a traditional planetary gearbox, but behind it is a servo motor that drives the gearbox and gives you 100 percent torque from zero speed. What that means is as an operator I have full torque all the way through the range of power versus diesel. Amazing for grading, for digging the piles.”
According to Berg, adjusting performance for different tasks will very rarely require changing whole systems like on a hydraulic platform, since an electric track loader’s servo motors and actuators are software configurable. Settings for the actuators’ stroke length and speed can be changed by updating the software, similar to installing the latest firmware update for a PC. There is also no topping off hydraulic fluids.
Its lift has an IMU sensor (right) that reports distance tilted or lifted back to the software. The CTL has electric actuators (middle) and not hydraulics to operate its lift (left). The battery box contains load-management technology designed to even out power usage to better conserve the charge over time, in addition to a gearbox that delivers battery power to individual servo motors on the tracks and lifters of the machine. Photos by Jeff Yoders/ENR
Trimble is taking a similar approach for customers to use their existing machinery fleets in new ways, offering upgrades to bring 3D machine guidance into the cab to help operators save time. While 3D machine controls and guidance have been commercially available for well over a decade, using them to get a grade in the cab and eliminating the need for a surveyor or other worker to hold grade stakes outside the machine still takes some getting used to. But being able to install a machine control system today for a minimal investment today compared to investing in a whole new machine, is changing contractors’ calculus.
Siteworks Machine Guidance uses Trimble Siteworks software for surveying and project layout to provide direction to the operator via an in-cab tablet display. A single excavator operator can perform activities that previously required a whole crew—with GPS units working alongside the operator, conducting surveying and in-field design tasks. Logging data on trenches dug or the exact number of buckets excavated can be done automatically as well.
“It’s helping the contractor, especially the smaller [companies] that I’d call the non-enterprise level—shops that are usually owner-operator—break into technology, and really be more productive,” says Steve DiBenedetto, Trimble product manager of civil construction and field solutions. Operators now "don’t have to be jumping in and out of the machine.” He notes that Siteworks Machine Guidance can also help contractors with personnel challenges, because they don’t need a separate person down in a hole with a stake for surveying work or have to call a surveyor back to the site when somebody knocks over stakes that were already placed.
Siteworks Machine Guidance can be installed in a few hours by a Trimble SITECH dealer. It consists of three parts: a Trimble GPS antenna that mounts to the top of the excavator arm; an inertial measurement unit (IMU) sensor attached to the dogbone of the excavator arm; and the field tablet in the cab. Along with a wiring harness, the system can be installed on any small to mid-size excavator, according to Trimble.
The IMU allows measurements such as depth and angle of dig to be uploaded to Trimble’s software in the cab. The GPS antenna brings those movements into context, including with a 3D model of what’s beneath the ground, using the Trimble software’s positioning engine. The sensor, GPS and IMU all connect via Bluetooth. The Trimble SPS986 or the Trimble R780 GNSS Smart Antennas are both available to use as the GPS antenna with Siteworks Machine Guidance. Trimble is selling Siteworks Machine Guidance as a subscription with monthly payments or in a more traditional perpetual offering. If a contractor already has a Trimble site positioning system running Siteworks, the upgrade could cost around $5,000 depending on regional dealer pricing.
Delivering pallets of polisilicon photovoltaic panels with autonomous CTLs saves labor on a solar project in Western New York. Photo left courtesy Moog Construction
“We’re using the system primarily on our smaller job sites,” says Tom Gardocki, co-owner of New Era Excavation in New Hampshire, who is also known for his “Dirt Ninja” YouTube channel, where he demonstrates various equipment he uses. “We’re Trimble users already, we run a lot of their other systems including 3D grade control on our excavators and bulldozers, and then we have multiple base and rover setups for 3D as well. So this is another tool in our kit, for certain jobs.”
Gardocki says New Era uses Siteworks Machine Guidance mostly on smaller drainage and grading projects where the job doesn’t warrant the time to build a full 3D model of the site. Instead, he just goes to the site, shoots the survey points, saves them into the base layout and brings them up on the Siteworks Machine Guidance tablet to get the guidance for excavation. “That’s the big benefit, you’re kind of getting the two systems in one, almost,” Gardocki says. “You don’t have the full capability you’d have if you invested in the full 3D system, but it’s definitely a great way to get started in 3D machine control.”
Gardocki says it can take as little as five minutes to define the points, get the machine set up and accurately dig with the guidance in the cab.
Like Moog and Built, Trimble has also found an eager market of contractors willing to use its technology in utility-grade solar projects.
When Trimble added a 1.7-MW field of solar panels to generate power for its Westminster, Colo., headquarters earlier this year, the contractor used Trimble Groundworks to identify and dig holes for the piles to support the solar array.
Using GPS coordinates, the Trimble Groundworks system finds the exact location for a pile and ensures accurate plumbness and alignment and proper depth. The traditional method, using string lines to align the posts, introduces risk of error and has longer set-up times, not to mention adding a tripping hazard for workers doing the measurement. Depth of a dig can be tracked by the angle and depth of the bucket as measured by the IMU and, with GPS coordinates, contractors are tipped off to conditions such as the site not being level or marked at proper elevations when they show up.
Trimble’s contractor “was very hesitant, honestly, to get into the technology and we, as the client, sort of forced [it] to use Groundworks,” DiBenedetto says, adding that soon after project completion, the firm "put in an order for four systems." He adds that the technology "really does help [the contractor] do the work. The same value proposition is there—faster, more accurate, with less skilled [workers] needed to help place the piles in the right spot.”
”Dirt Ninja” Tom Gardocki uses Siteworks Machine Guidance on small jobs to set up control points and measure accuracy of digging where full 3D modeling would not be cost effective. Trimble’s solution uses a GPS antenna, an IMU sensor and a tablet in the cab that connects to the antenna and sensor via Bluetooth. Photos courtesy Trimble, Inc.
Charging electric equipment remains a concern for contractors working in both remote areas and those simply without nearby charging stations. Even when power is readily available there is still competition for limited charging stations. As of now, the Bobcat T7X can be fully charged overnight from standard EV ports, but the Moog team believes they can get that down to a full charge in four hours when using their proprietary chargers.
“We have a fast charger, it can pump your [equipment] full much quicker than most other electric machines, which takes anywhere from like, four to 10 hours to charge,” Moog’s Berg says. “The runtime is about half a day, but because of how quickly it can be charged we have a concept of opportunistic charging where we could recommend, after a safe morning shift, you plug the equipment in for 10 to 15 minutes and then go have lunch. We’ll get it back up to enough to finish the rest of the day during lunch. It’s not as much of a pain and inconvenience as opposed to having to drag it somewhere to charge for eight hours.”
Like Trimble, Moog is also pursuing solutions that can take existing equipment and give it new capabilities with an aftermarket installation. Moog has developed an electrical battery box that can be bolted onto any small to mid-size excavator with four bolts, two connectors on the sides and a wiring harness that can turn any OEM excavator into an fully electric one. Berg says the firm can also make tele-operable the machines that use the large Moog battery pack because the wiring harness is connected to the in-cab joysticks.
Equipment manufacturers who work with Moog, Trimble and Built are competing for contractor business, but big players such as Komatsu, Caterpillar and John Deere are all committed to shifting production toward electrical machines, so they also have an incentive to work with middleware providers to bring their customers along on this journey.
New Era’s Gardocki says that solutions that meet the contractor halfway and simplify repetitive tasks are what the bulk of the market—small-to-mid-size contractors such as his firm—will continue to need from their machines through a transition still in its infancy.
“I just think we’re a very, very long ways away [from autonomous machines],” Gardocki says. “Certain tasks, obviously, are simpler than others, but you’re talking about construction, where things change constantly, and you run into issues and you’re running into an underground ledge and you’re running into other buried things. To get a robot smart enough to do that, I think it’s going to take quite some time."
He adds, "These systems that simplify tasks to [require fewer] people but still leave an operator in charge are going to be what everybody is looking for, at least over the next 10 years or so.”
You must have JavaScript enabled to enjoy a limited number of articles over the next 30 days.
Copyright ©2023. All Rights Reserved BNP Media.
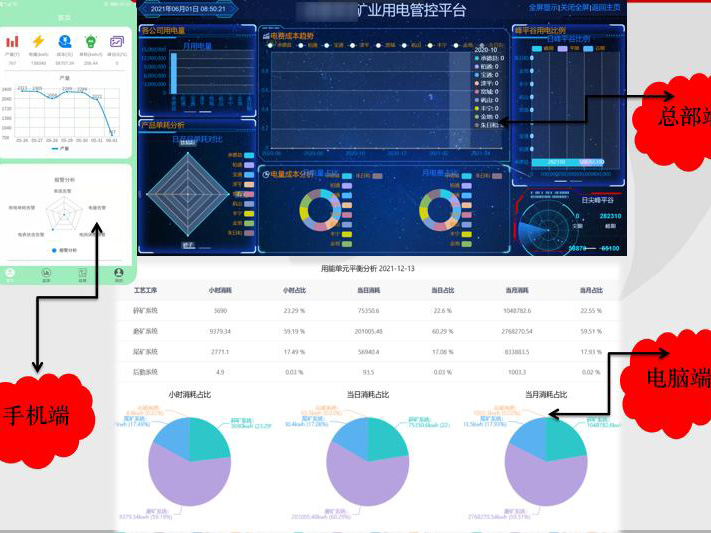
Large Angle Corrugated Belt Conveyor Design, CMS, Hosting & Web Development :: ePublishing