211 Kitty Hawk Drive Morrisville, NC 27560 US 800-772-4865 | 919-572-2705 info@us.schunk.com us.schunk.com
Do you have a new product or news release that should be included here for SCHUNK, Inc.? We'd love to include it! Send your content to our editorial team. Sanou Lathe Chuck

Almost any shop can automate at least some of its production, even in low-volume, high-mix applications. The key to getting started is finding the simplest solutions that fit your requirements. It helps to work with an automation partner that understands your needs.
Automation Explorer will enable users to interact with Schunk automation technology in an immersive and detailed, physics-based simulation tool.
The 5-Axis Live technology event will highlight new machining strategies for optimizing the production of complex medical, aerospace and mold/die parts.
Automation headlined BI-MU 2022, while flexibility underscored exhibitors’ products. These twin benefits may be shops’ greatest assets against inflation.
With the new SCHUNK tools for machining with the robot, workpieces can be ...
With the new SCHUNK tools for machining with robots, tasks that were previously carried out manually can be...
The robust electric universal gripper EGU is resistant to dust and cooling lubricants thanks to its IP 67 seal.With his ...
Intelligent grippers, autonomous milling machines or self-learning cobots – SCHUNK stands for innovative technologies that...
With the new SCHUNK tools for machining with the robot, workpieces can be ...
With the new SCHUNK tools for machining with robots, tasks that were previously carried out manually can be...
The robust electric universal gripper EGU is resistant to dust and cooling lubricants thanks to its IP 67 seal.With his ...
Intelligent grippers, autonomous milling machines or self-learning cobots – SCHUNK stands for innovative technologies that...
Understand Machine Tending Solutions to Simplify Automation Solutions
This webinar will break down and simplify automation solutions to help you understand which machine tending solution is right for you and how to maximize your manufacturing process efficiency.
Targeting two-to-four hours of nightly automation enables high-mix manufacturer Wagner Machine to radically boost its productivity past a single shift.
Robotic automation relies on reliable workholding, and these modular pneumatic jaws make it simple.
Hyprostatik Schönfeld’s product range includes lead screws with hydrostatic nuts, guide shoes, tailstocks, spindle bearings and rotary tables in different sizes and designs.
By taking inspiration from gecko feet, Schunk has developed a residue- and particle-free adhesive robotic gripper that holds up to 35 pounds.
Automotive dies and die inserts are often complex, one-off parts with little room for error. Integrity Tool's investments in modular workholding tools and 3D optical scanning have allowed the company to create niche capabilities for its CNC machined parts.
Schunk says its Rota THW3 quick-change jaw chuck is particularly beneficial for users who produce small and medium quantities and are frequently switching between jobs.
Schunk’s CoLab is designed to be a working space for technicians and engineers to collaborate with the Schunk team and partners on their specific applications.
Schunk’s Rota-M Flex 2+2 chuck jaw is designed to provide increased flexibility for clampable workpiece geometries and a variety of possible applications.
Schunk claims its toolless jaw quick-change system reduces setup times to a minimum, therefore increasing the productivity and flexibility of the entire system.
Constructed of durable hardened tool steel, the Tendo Platinum V2 reportedly improves stability, stiffness and clamping force to support sustained accuracy throughout its life.
Norgren’s Adaptix Soft Jaw uses adjustable fingers and interchangeable tips to grip a wide variety of parts or workpieces during the CNC machining process.
Schunk says the technologies included in the THW3 chuck result in high process reliability, quick jaw changes, constant clamping forces and long maintenance intervals.
Schunk’s EMH electro-permanent magnetic gripper has a compact, energy-efficient design.
A sensory toolholder can provide more accurate vibration data on the metalcutting process, helping to extend tool life and improve surface finish.
Schunk’s Rota-M flex 2+2 chuck jaw offers a level of flexibility that the company says is unmatched on the market and covers a wide range of part geometries.
Schunk’s Tandem PSG3-LH 100 clamping force block provides a low-maintenance solution for transitioning into automation for basic aluminum and plastics machining applications.
The Schunk iTendo toolholder records metal cutting processes, monitors previously defined limit values and enables real-time adaptive control of rotation speed and feed rate.
Allan Logan has more than 20 years of industry experience and has been with Schunk since 2018.
Schunk’s Vero-S NSE Mikro 49-13 is a completely sealed miniature clamping module specifically for metalcutting, assembly, handling and measurement applications.
Schunk now offers a version of its Tendo Slim 4ax with Cool-Flow coolant-through technology.
The Rota NCR-A, a sealed six-jaw pendulum compensation chuck from Schunk, is designed with seals at the jaw interface and the piston to keep the grease from being washed out.
Instead of investing in an external robotic loading system, this shop adopted technology that lets a machine tool load parts on its own.
The Schunk Kontec KSC clamping vises are made for raw and finished part machining.
The new facility, combined with investments in personnel and equipment over the next five years, represents another $60 million for the region’s economy and roughly 100 new jobs.
Schunk’s PGN-Plus-P gripper features enlarged supporting dimensions between the six load-bearing shoulders of the multi-tooth guidance, allowing higher moment capacity, in turn accommodating longer fingers and greater loads.
Shops take some modern robot capabilities as given, but a recent trade show in Japan demonstrated ways those capabilities continue to improve.
IMTS 2018: The Schunk Vero-S Aviation product line is designed to rigidly clamp large parts accurately and enable the user to release the part enough to allow the part to move (compensate) due to the stresses of machining without fully releasing the part.
Safety standards, third-party certifications, plug-and-play packages and new sensor technology for grippers designed for collaborative robots are making them safer, stronger and easier to use.
The Schunk Vero-S Aviation product line clamps large parts accurately, enables the parts to be moved, and establishes data points through four modules.
The jaw design of Schunk’s UVB-HS soft chuck jaws provides efficient gripping for lathe workholding.
The Schunk Vero-S WDB modular clamping system provides the efficiency levels of the Vero-S quick-change pallet system to machine directly clamped workpieces.
The Rota-S Flex from Schunk is a flexible manual chuck for machining a variety of workpieces on milling and turning machines.
A flexible robotic part-loading and unloading system enables a small Indiana shop to boost production without a large investment.
The Tendo Platinum toolholder from Schunk is designed for durability, ease of use and precision for many milling, drilling and reaming applications.
The slim design of Schunk’s Tribos-SVL toolholder extensions enables precise and smooth machining of difficult-to-access workpiece areas while providing a runout accuracy of less than 0.003 mm, according to the company
Schunk to add square footage and jobs to its U.S. headquarters, a pre-apprenticeship program for women commences 11 graduates, and other industry news.
Schunk’s Rota TB2 pneumatic self-contained power chuck features a new design to reduce maintenance costs and ensure process reliability.
The two phases of the project will add some 19,000 square feet of manufacturing space and 22,000 square feet of tech center, training and office space by the end of 2018, expanding what is already the company’s largest facility outside of Germany.
Schunk Magnos parallel pole, square pole and radial pole plates are designed to ensure reliable workpiece clamping, quick workpiece changes and efficient grinding.
Bo Shomaker has 27 years of experience in the metalworking industry, with his most recent positions involving sales management for Southeast Asian customers.
Schunk’s Tribos-Mini precision toolholder, designed for micro applications, is now available for the HSK-E 20 high-speed spindle interface.
Schunk’s Vero-S NSL quick-change workholding and positioning system is designed to speed setups with the ability to mount any workholding on top, from a standard vise to a custom fixture, for reliable and consistent change-over.
The center offers a range of services to local manufacturers.
Grippers and end-effectors developed specifically for collaborative robots represent new advancements in this type of robot technology.
Schunk’s Tendo E Compact toolholder eliminates the need for different holder technologies for milling, drilling and reaming.
Schunk will exhibit the Rota NCX, a power lathe chuck with quick jaw-change system.
Schunk is expanding its line of hydraulic expansion toolholders with the Tendo Aviation designed for demanding applications such as those commonly performed in the aerospace industry.
This investment casting company doubled production of a series of parts by incorporating workholding into a cell that keeps pallets constantly moving across the machine tool.
One of the speakers, a second-year apprentice, is in the middle of an apprenticeship with Schunk.
Schunk’s Tendo Platinum toolholder for milling, drilling and reaming is made using a single-cycle brazing and hardening process, enabling rigid and durable tool clamping.
Schunk’s Gripper with Spindle Interface device enables a machine to load and unload workpieces on its own. See how.
The Schunk Prismo3 toolholder for tool grinding directly clamps shank diameters between 3 and 20 mm without the use of collet chucks or sleeves.
Schunk’s Magnos magnetic chuck enables all five sides of a workpiece to be machined simultaneously in one setup.
The SVP-Mini and SVP-RM manually actuated clamping devices from Schunk are run on factory-defined set pressure.
To get the most potential out of its multitasking machine, Trumpf uses a detailed custom clamping concept from Schunk.
This system uses the standard Weldon flat so that end mills do not have to be modified for locking in place when a precision toolholder takes high-force cuts.
Designed for use with Schunk's Vero-S quick-change pallet system, the Vero-S SPM plus 138 diaphragm clamping module is machinable to accommodate the contour of a specific workpiece.
Schunk’s Tribos-RM precision toolholder features an ISO interface and is well-suited for holding the small tools used in micromachining operations.
The tooling and workholding suppliers hosted a combined event in early April.
Schunk’s Tribos-SVL toolholder extension enables precise, smooth machining of workpiece areas that are difficult to access.
The Rota NCR six-jaw power chuck from Schunk is designed for machining thin-walled, easily deformed workpieces.
The NSL series of Schunk’s Vero-S system enables shops to quickly and easily implement a quick-change pallet system with a universal standard.
Schunk’s Rota THWplus quick- jaw-change chuck is designed for flexibility and efficiency in setups.
Schunk's Tribos-Mini directly clamps small tool shanks consistently along the entire axis for challenging applications including medical, dental and micro-level parts.
Schunk’s Tendo Platinum toolholder is designed for durability and precision in most milling, drilling and reaming applications.
Schunk’s Kontec KSX NC vise for simultaneous five-axis machining is designed to handle tool-free adjustable clamping forces between 4 and 40 kN measured directly at the workpiece.
The Schunk Vero-S quick-change pallet toolbox features functional components made of hardened stainless steel, including the base body, clamping pin and clamping slide.
The company opened its U.S. headquarters in Morrisville, North Carolina in 1992.
Using lean manufacturing’s A3 problem-solving process, Genesis Attachments found that magnetic workholding could provide greater benefits than simply getting parts on and off machines faster.
Schunk’s Tandem KSP+64 is said to be a major development in miniature, self-centering clamping technology.
Schunk’s Tendo E compact toolholder is designed for milling, drilling and reaming applications.
Schunk’s Tribos-Mini toolholder directly clamps small tools for challenging applications, including machining medical, dental and micro-level parts.
Schunk’s Prismo holder for automated tool and cutter grinding is designed to clamp diameters ranging from 5 to 20 mm without additional components or change-overs, and features repeat accuracy of less than 0.005 mm.
Automated machining processes enable this maker of high-performance mountain bike parts to manufacture efficiently with minimal staff.
Schunk’s Tendo E compact hydraulic expansion toolholder is designed to eliminate the need to use different holder technologies for milling, drilling and reaming.
Schunk says its technology offering at the upcoming imX (interactive manufacturing experience) industry event will focus on automated solutions that increase manufacturing efficiency on a large scale.
The Tribos-Mini toolholder from Schunk directly clamps small tool shanks along the entire axis virtually eliminating collets, collet nuts and inconsistent cutting tool clamping.
The Tendo hydraulic expansion toolholder offers high-precision shank tool clamping suitable for high speed machining; heavy-duty milling; internal grinding, boring and chamfering; reaming; and tool grinding.
Schunk’s TENDO E hydraulic expansion toolholder is suited for high-volume cutting.
For exact machining of thin-walled rings on rotary tables, cylindrical grinding machines and lathes, Schunk offers standardized magnetic chucks with radial pole pitch.
Schunk says its hydraulic expansion extension Tendo-SVL transforms virtually every precision toolholder into a highly versatile specialist for narrow spaces independent from the spindle interface.
Lockheed Martin’s precision machining of composite skin sections for the F-35 provides part of the reason why this plane saves money for U.S. taxpayers. That machining makes the plane compelling in ways that have led other countries to take up some of the cost. Here is a look at a high-value, highly engineered machining process for the Joint Strike Fighter aircraft.
Schunk says its Sino-R toolholder is maintenance-free and well-suited for rough milling applications.
The vibration-damping capabilities of Schunk’s high-precision Tendo-E hydraulic expansion toolholder are said to increase tool life, improve surface quality and minimize stress on the spindle. The toolholder can be changed without additional peripheral equipment and features an axial length-setting screw for quick tool-presetting.
Shunk’s Celsio shrink-fit toolholders offer the flexibility to combine various shrinking chucks and extensions. This minimizes the number of chuck bodies required to provide a range of diameters.
Joe Gibbs Racing applies a number of workholding techniques to speed the production of racing components its engineering team creates every day.
The Schunk Tendo-ES is a short, hydraulic-expansion toolholder that allows the tool to be clamped directly in the mounting taper. The tool shank is supported via the spindle, and the result is a high holding force for transferable high torque and additional space in the machining area.
This footage shows a workpiece gripper that enables a machine to load and unload workpieces on its own.
A workpiece gripper that installs in a machine tool's spindle enables the machine to serve as its own robot.
Magnos magnetic clamping technology can be used in conjunction with the Unilock quick-change pallet system to increase flexibility and to reduce setup times and cost. According to the company, magnetic workholding provides high holding forces and allows the spindle to access five sides of a part. Pole extensions that act as workpiece supports allow the user to position different workpieces rapidly and precisely, the company says, which improves the productivity of the machine.
Heinz-Dieter Schunk, CEO of Schunk, was awarded the German Machine Development Prize at the third German Machine Development Summit in Berlin last October. At the summit, an independent jury of experts in business and science recognized Mr. Schunk’s lifetime achievements.
Schunk’s Tandem KSP plus stationary clamping system achieves a repeat accuracy of up to 0. 01 mm with the multi-tooth guidance of the base jaws, the long jaw guidance and the exact centering via the clamping sleeves which help reduce jaw lifting. The compact, clamping force block, which features a one-piece, rigid base body, achieves gripping forces ranging to 60kN.
The Tendo family of hydraulic expansion toolholders from Schunk now comes in a super-slim version. The Tendo LSS has been optimized to keep interfering contours to a minimum. It can be used to access difficult parts of a workpiece and function in working areas where appliances create difficult conditions. The tool
Schunk’s SRH 180-degree swivel heads are completely modular in structure and consist of SRU rotary modules combined with two swivel corners, EDF electric feed-throughs and MDF media feed-throughs. These components are intended to produce precise rotation and long tool life. Using standard components also means shor
A combination of toolholding choices lets this die shop get the most performance from its small-diameter tools.
An alternate toolholding technology has allowed a shop to achieve much higher spindle speeds on an HMC used to machine short runs of aluminum billet workpieces.
Through a sweeping transition to high speed machining, a Maryland contract shop realizes its goal of same-day, "in by 9, out by 5" turnaround.
This toolholder employs expansion technology similar to that used by high-end hydraulic toolholders at a cost comparable to collet-style toolholders.
Any shop with CNC machine tools has probably wondered how a DNC system could be configured to operate with wireless network connections. Wireless systems are being installed in offices, and even in homes, so that laptops, desktop PCs, and handheld devices can communicate via e-mail, share access to the Web, and exchange data.
The book on hydraulic toolholders is that they are fussy to set, fragile to operate and expensive to buy. So why do many shops choose them over other holders that seem less demanding? This Chicago mold builder has good reasons for its choice.
One of the neat things about metalworking is the wide variety of solutions generated for specific challenges. Shrink fit tooling is one such challenge. Much has been written and demonstrated about the advantages in concentricity, balance and ultimately accuracy that such tool-holders bring to the machining process.
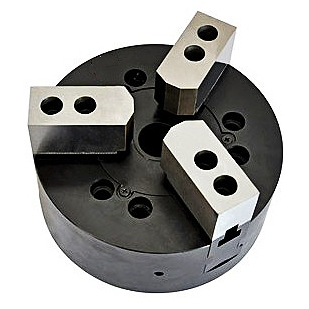
Soft Jaws For Lathe Connect with us to keep your company's information up to date.