Structural Insulated Panels (SIPs) are self-supporting panels that consist of a rigid foam core sandwiched between two structural coverings, typically OSB boards. These panels are lightweight and durable, and they are produced in a controlled factory environment before being transported to the construction site. They can be quickly assembled to form floors, walls, and ceilings, creating a tight thermal and acoustic envelope. The panel's thickness is determined by the combined thickness of its components, and its weight should not exceed 20 kg per square meter.
Although designers will most commonly use SIPs with two claddings and an insulating core—supporting dead loads of up to 5 kg/m2 and live loads of more than 30 kg/m2—there are options that include additional wooden frames to increase rigidity. This high mechanical resistance is achieved by adhering the panel's different components with polyurethane emulsion. In addition, each panel can include cavities for the passage of installations and other ducts. Thanks to the prefabrication, it is estimated that the use of SIPs can reduce construction times by more than 50% as compared to traditional methods, also eliminating a large amount of waste typical of on-site construction. Sandwich Panel Walls Price
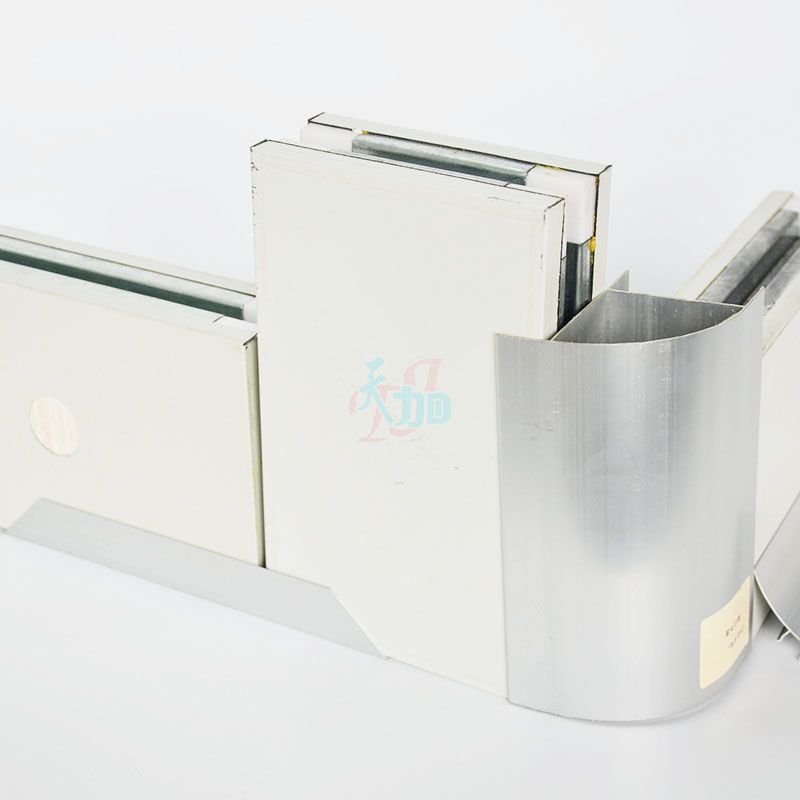
However, each project is different and it is important that the composition and dimensions of the SIPs used are adapted to these particularities, from the requirements of the inhabitant to the climatic conditions that they will have to face. In terms of fire resistance, both the outer coatings and the insulating core must comply with local regulations, incorporating materials and/or additives that delay the generation of flames. Regarding the installation process, the simplest method is to mount the modules on wooden sills, joining the different panels with glued slats of a smaller dimension.
Let's review the successful application of SIPs in real cases of residential architecture. In the case of the Shotgun House—designed by Alejandro Soffia in Cachagua, Chile—the SIPs embody the architect's intention to adopt a replicable construction system that delivers the benefits of high-quality architecture at a massive level. According to the architect, "to take advantage of the prefabricated systems, in this case, the bays strictly respond to the multiplication of the module as it comes from the factory. In this way, materials and processes are reduced, resulting in cost and time savings." In its width, the house is made up of 33 panels of 4.88 meters, adding up to 40 meters in length and a total area of 426 m2. "The base ‘bay’ optimizes the measures of the panels, and it’s been modified according to the different programmatic requirements," he adds.
Also in Chile, La Dacha Mountain Hut builds its entire perimeter with SIPs 21 centimeters thick, providing a lightweight solution for remote construction, but ensuring optimal thermal insulation. The panels form continuous walls around much of the volume and are clad with burnt pine boards (shou sugi ban) on the outside.
SIPs can also be merged with other construction solutions. In the El Tume House by abarca+palma, the panels were integrated with wood carpentry that allowed for the construction of the foundation pillars, the beams, the interior and exterior partitions, the coatings, and the floor. In this case, the SIPs are externally clad with untreated Oregon Pinewood, which will turn gray over time.
The architects of abarca+palma explored the same mixed solution in the House in Alto Grande, joining the woodwork and the SIPs to "generate a modular coordination between all its construction elements." The panels are covered in this project by zinc plates.
Systematizing the construction process according to the assembly process of the prefabricated materials, the Hats House took 5 months to be built. The SAA architecture + territorio team incorporated SIPs in the envelope of the floors, walls, and ceilings, covering them on their visible side with native wood with a rustic appearance.
For the Origami House, the Mas Fernandez Arquitectos + OR Arquitectos team used SIPs covered with treated pine wood to guarantee adequate thermal insulation for the envelope. This construction system was mixed with a metallic structure for the widest spans of the project.
Oller Caracas House mixes exposed concrete with walls, partitions, and ceilings in SIPs, externally clad with tin and internally with wood.
The team of Benjamin Goñi Arquitectos and Claro + Westendarp Arquitectos chose SIPs as the main construction system of two twin houses in southern Chile due to their good thermal insulation. The modular system allowed them to add traditional elements of the architecture of the area, and "instead of making eaves as a roof finish, frames are built in the openings of the windows, in order to keep the rain away from the windows."
In their design for the Lerida House, the architects Cristian Yazigi and Crescente Böhme Alemparte used SIPs to expand and renovate a house from 1970. "For the intervention on the first floor, it was chosen to build from the existing materials of the house, including reinforced concrete and masonry walls, while the second level is built from SIPs and a ventilated wooden façade."
Externally wrapped with black quadroline metal panels, Cristián Romero Valente's WV House is made up of a metal structure that shapes its walls and ceilings. To insulate them thermally, interior skin and SIPs have been added to the exterior, eliminating thermal bridges and incorporating a high-performance heat recovery ventilation system.
Find more projects built with SIPs here.
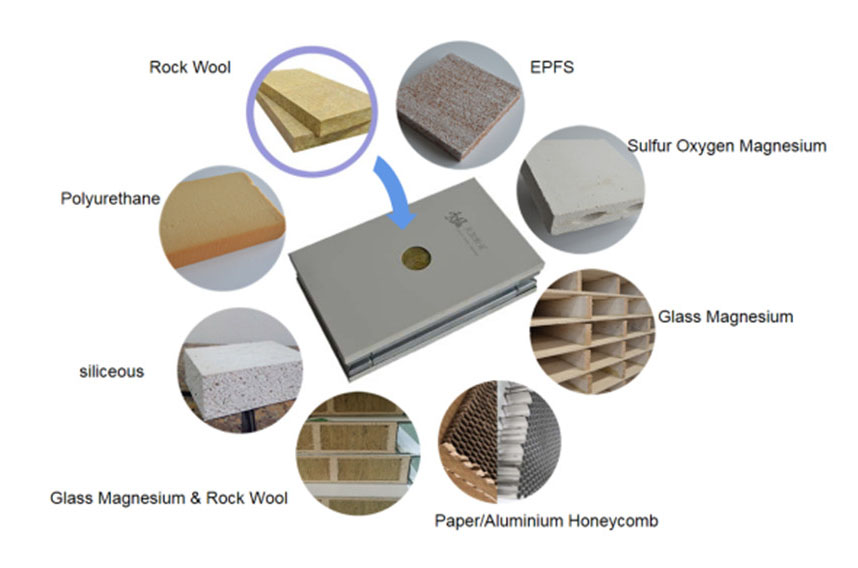
Cold Room Sandwich Panel You'll now receive updates based on what you follow! Personalize your stream and start following your favorite authors, offices and users.