When you purchase through links on our site, we may earn an affiliate commission. Here’s how it works.
The P1S hits a sweet spot, offering affordable Core XY speed for a wide range of materials and access to Bambu Lab’s popular AMS system to print in up to 16 colors. Aisi 316 Stainless Steel Coil

Enclosure for high temperature printing
Why you can trust Tom's Hardware Our expert reviewers spend hours testing and comparing products and services so you can choose the best for you. Find out more about how we test.
Bambu Lab is at it again, producing a near-perfect printer that impressed us with its speed, quality and ability to handle a vast array of materials. The P1S is a less expensive version of the very popular X1 Carbon, a deluxe 3D printer that introduced the masses to effortless Core XY speed in 2022.
Shockingly, the P1S doesn’t bring any technological improvements to the table. Rather, it offers users a set of features they crave: a fully enclosed, easy to use Core XY printer that doesn’t break the bank. Retailing at $699, the P1S is $500 cheaper than the deluxe X1 Carbon, which has more sensors, a better screen and a higher quality camera.
The introduction of the P1S has slashed the stripped down P1P to $599. To appease any sense of buyer’s remorse, Bambu Lab is offering a P1P to P1S upgrade kit for $150. This includes plastic panels, a glass door and top cover plate, heavy-duty toolhead cable and chain, and cabin fans. The P1P famously offered “print it yourself” side panels.
The price tag is still high compared to some of our favorite budget 3D printers, but much easier to afford than the esteemed Prusa MK4 or fun to watch FLSun V400. The P1S has one of the best auto bed leveling systems, input shaping, a PEI coated flex plate, linear rods and a self-cleaning tool head. It’s capable of 500mm/s print speeds with a blazing 20,000 mm/s acceleration speed, making it our favorite speedster and one of the best 3D printers we’ve seen.
The Bambu Lab P1S comes with everything you need to get your printer set up, as well as a few extra parts. You get tools to maintain the printer, a spare hotend, two spare nozzle wiping pads, and a microSD card. There’s also a sample of green PLA on a full sized, reloadable spool.
The microSD card contains several test models. A razor blade and screws are included to make a DIY scraper from a file on the microSD. There’s also a paper getting started guide and instructions on how to access the slicer and phone app. The box has a QR code printed on the inside flap that leads to an unpacking video.
The P1S is the budget model of Bambu Lab’s deluxe X1-Carbon 3D printer. It is fully enclosed with plastic sides – rather than aluminum – and shares the same D-pad selector interface as the P1P.
It’s the 3rd Core XY printer brought to us by Bambu Lab – all three share the same motion system, build volume, speed and quality. Core XY printers use a combination of belts to move the X and Y axis in tandem for smoother, faster printing. The print head stays at the top of the machine while the build plate slowly lowers. When combined with vibration damping input shaping, the results are exceptionally smooth, high quality prints.
The printer’s highly sensitive auto bed leveling system makes for a perfect first layer. There is no way or even need to adjust the z height. After a few minutes of auto calibration the printer just works.
The P1S is compatible with Bambu Lab’s now-famous, four-color Automatic Material System. The optional AMS is $349 dollars and perches on the printer’s glass top. It supplements the rather annoying rear mounted spool rack, which I quickly replaced with a table-top spool holder to sit in a more accessible spot next to the printer.
The P1S needs a collection bucket for its community-dubbed “poop chute” which is also in the back. Even if you don’t use multicolor, the machine will purge filament into a waste chute before every print. I printed a slide style chute that brings filament waste to the side of the machine.
The P1S comes equipped with an all-metal hotend and long-lasting .4mm stainless steel nozzle. The nozzle itself is not replaceable – you need to swap out the entire hotend if it gets worn down. This system is not as easy as a quick change E3D Revo, and involves several screws, plugs and very delicate thermistor wires. If you want the option of switching between nozzle sizes, it’s advisable to purchase complete hotend assemblies. Fortunately, these are reasonably priced at $9.99 for a stainless steel hotend and $34.99 for the complete assembly.
All the printer’s parts are custom and need to be purchased directly from Bambu Lab. The web store appears to cover every part, from thermistors to belts, so at least customers are not left wondering if 3rd party parts will fit.
You can upgrade a P1P to a P1S but you can not upgrade a P1S to an X1-Carbon. The LiDar sensor, camera and touchpad were not made to work with the cheaper printer’s boards.
Bambu Lab says its printers can obtain a top speed of 500mm/s and 20,000 mm/s acceleration. However, that’s twice the default speed of the printer. Instead of fiddling with complex settings to go high speed, you only have to hit the “turbo” button. Once a print is sent, you have the option of bumping it up from standard to “sport” or “ludicrous” speed, which is 124% and 164% faster than normal. You can access the speed settings from the slicer or the printer interface.
While most things work fine in sport or ludicrous mode, not all materials can melt fast enough to keep up with these speeds. The slicer’s material profile contains a hidden throttle: the Volumetric speed limitation. This number is the volume of filament that can be extruded per second. This means a “ludicrous” TPU print is a lot slower than a “ludicrous” PLA print.
Why not run ludicrous all the time? Bambu printers lose some surface quality when pushed to the max, some materials lose their shine and layer adhesion suffers making for weaker prints. We’re also certain that all that violent movement can’t be good for the printer’s longevity.
When the P1S does have an error – even the best printers can choke – it tries to help you diagnose the problem by issuing an error code. The code will appear on the printer’s screen as a long scroll of unhelpful numbers. But the error code will also appear on the phone app and the device tab on your computer. These codes are links to the Bambu Wiki, a knowledge base for operating any Bambu printer. The Wiki will help you identify and fix the problem, often with quick video tutorials.
One of the major advantages of the P1S is its compatibility with Bambu Lab’s AMS system – a four spool feeder that unlocks the ability to print in four, eight, twelve and even sixteen colors. The units cost $349 each and can be placed on top or next to the printer.
The AMS unit is able to read RFID ID tags the company installs on each roll of its own filament for easy identification. These tags tell the printer what type and color of material you have installed, and then matches it with presets in Bambu Studio. If you use 3rd party filament, you’ll have to fill that information in by hand.
The Bambu Lab Studio is all you need to digitally paint your models with color. While reviewing the P1P I documented a single color model of a toy horse I converted into a buckskin, including all the wasted filament. This has not changed. You can read more about the AMS in that review.
The AMS has pockets for descant and seals tightly, allowing you to use the AMS as a drybox for temperamental filament like Nylon. An indicator on the Device tab of Bambu Studios lets you know when it's time to dry out your descant packets. When I took this screenshot, the symbol was orange, warning me it’s time to switch.
There’s also a “backup” option for the AMS which will allow it to automatically switch from one slot to the next instead of tripping a run out sensor. This could be handy for using up partial spools or prints that will need more than one spool. To use this setting, you’ll need to have identical spools loaded.
The Bambu Lab P1S comes mostly assembled and only needs to be unpacked. You only need to attach the spool holder and control screen. The printed guide walks you through each step.
The Bambu Lab P1S has an excellent auto leveling system combined with vibration compensation, pressure advance and semi-automatic belt tensioning. A thorough self test is run after unpacking the machine to make sure everything is in working order.
Once you’re up and running the machine will automatically run a bed leveling check before each print. This takes about 6 minutes, but you’re free to uncheck the option if you don’t want to take the time.
There is no need to set the z height or z offset. In fact, there’s no option or button to do so, because the P1S handles this setting on its own.
For all its advanced features, loading filament without an AMS unit is tedious at best. The control screen is a confusing mess of cryptic symbols. First heat up the hotend (click the down arrow with waves) then load the filament through the reverse Bowden tube until it stops at the hot end. Then you push the advance filament button (the arrows and with an E) several times until it comes out of the nozzle.
To unload or change colors, there is an unload option that handles everything.
If you opt for an AMS unit, filament loading and unloading is handled by the machine. You only push filament 2 cm into the feeder and it automatically slurps it into the system.
Bambu Studio is the custom slicer for the P1S and its fellow 3D printers. It’s largely based off of PrusaSlicer and should feel very familiar to Prusa fans, though as a Cura user myself there was a bit of a learning curve. Fortunately, there are easy to use presets for all types of filament that work very well.
Bambu slicer will work with other printers and has a growing list of presets for Voron, Creality, AnkerMake, Anycubic, Elegoo, Prusa, Qidi and Voxelab.
Like PrusaSlicer, Bambu Studio has a tool for coloring prints. It’s a fairly simple painting program and you don’t need to be a designer to sort it out.
The device tab is where you can send files via Wifi, watch video from your camera’s timelapse and remotely tweak the speed and temperature of your printer.
You can also save complex builds in the project manager, which will then create a single 3mf file you can share. This file can include several plates of build parts, photos and a bill of materials.
Our P1S review unit came with a partially filled spool of green Bambu Lab PLA. This is great to get you started, but you’ll want to check out our guide to the best filaments for 3D printing for more suggestions.
The printer also came with several pre-sliced files to print. But I’m most interested in how the printer worked with files I sliced myself.
Here’s a couple “speed Benchy” models, which is the popular 3D Benchy sliced according to the official #speedboatrace contest rules. These boats have 2 walls, 3 top/bottom layers, 10% infill and use a .25 layer height and .5 layer width. The boat on the right was printed at 500mm/s in 18 minutes and the one on the left was printed using the normal speed of 200-300mm/s in 26 minutes. Input shaping is really doing it’s job on these prints, as there is no noticeable difference between the two. These are by no means perfect – gray is a brutally unforgiving color for the camera – but you can see the cooling along the steeply curved front is perfect, and the layers are very neatly stacked on the cabin. Both models are printed in ordinary Inland Grey PLA .
The printer was able to tackle “filament painting” with HueForge without having to switch to a super fine nozzle. The P1S auto leveling system gives a perfect first layer, which makes working with .08 thick layers easy with the stock .4mm nozzle. The AMS also lets me “paint” with four colors without manual color changes. This Baby Yoda painting took 2 hours and 36 minutes to print using Polymaker LM Sparkle Green and Christmas Green PLA Pro, Bambu Lab Green PLA, and 3D Fuel Lulzbot Green PLA+. The results are super smooth.
You don’t need to make multicolor prints to appreciate the usefulness of the Bambu Lab AMS as a handy spool holder. This action figure was made using eight colors, with each part printed individually on shared plates. I only had to swap colors once – when I changed the palette of colors. This saves a lot of time compared to running eight batches on single color machine. It’s also eight hours faster – and less wasteful – than if I ran all the parts using four colors at once with swaps and purges.
The action figure was printed using .16mm layers and 3 walls which resulted in buttery smooth layers, taking 2 hours, 43 minutes to print in two batches. The calibration dragon took 23 minutes to print using .2mm layers and 3 walls. These prints are using Bambu green PLA, Inland Blue, Black, White and Light Brown PLAs, Polymaker Starlight Jupiter (hair), and Protopasta Double Espresso (pants).
Since the P1S is enclosed, I had to try some practical prints with engineering grade materials. These are gears for a new RC controlled “Death Racer” car we’ll be competing with at the East Coast RepRap Festival. I need these parts to be strong and unbreakable, so I picked Matterhacker’s Pro Nylon.
This is where I also learned that nylon looks great when printed at high speed, but suffers from weak layer adhesion. Once the print was slowed down to 75mm/s on the walls the prints came out perfectly strong. These are also beefy prints, with 7 walls and 6 top/bottom layers. One tall gear took 1 hour and 13 minutes to print. There’s some interesting fuzziness along the shaft, but I’m not sure what was the cause. I only used a bit of glue stick on the PEI plate and the gears suffered no lifting or warping.
It had no problems with recycled PETG, which seems to work better than new PETG on high speed printers. This Greengate Amethyst printed using the default settings and a .2mm layer height in 1 hour and 52 minutes with smooth layers and just the tiniest wisps.
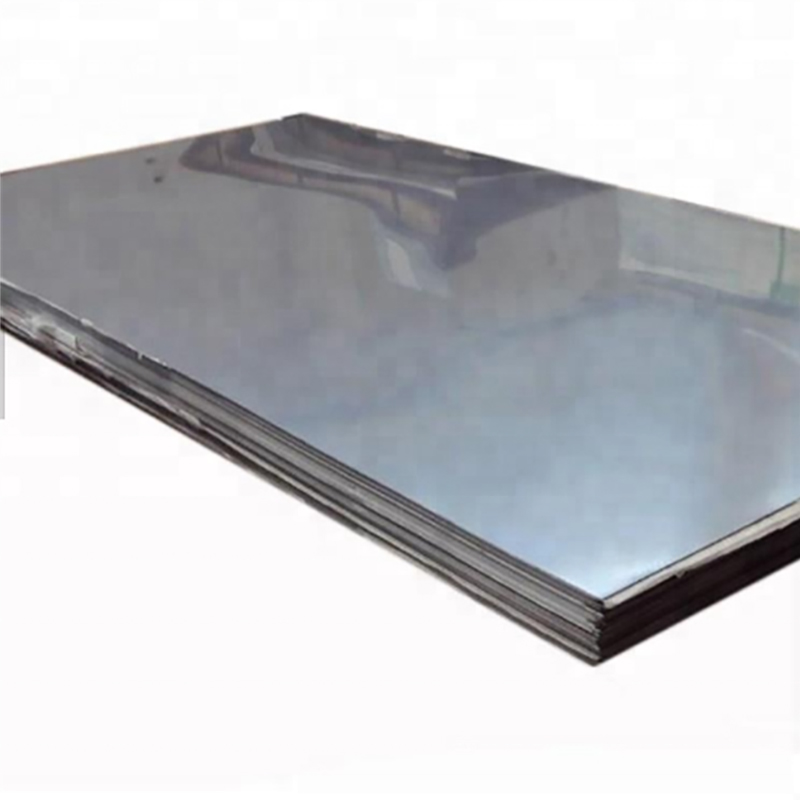
202 Stainless Steel Coil I also tested ASA with this handy tape dispenser. The fit was tight, but the parts are so sturdy I was able to bang them together with a hammer. This part printed smooth and without any warping, using just a bit of glue stick. Printed with .2mm layers with Polymaker Galaxy ASA using the default settings in 1 hour and 17 minutes.